Founded in 2000, Tellart is a design-driven, future-focused design studio that creates interactive experiences that move between digital and physical spaces. We spoke with Tellart’s head of strategy, Andrew Haarsager, about how 3D printing has found its way to the studio’s design process as well as the things it makes.
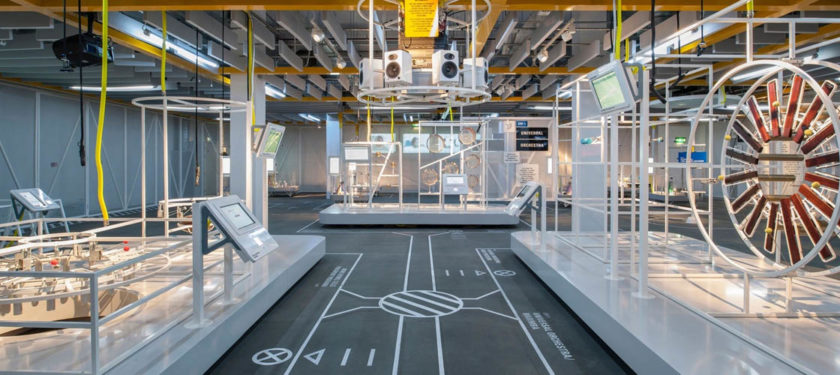
The Chrome Web Lab exhibition created by Tellart in collaboration with Google Creative Lab; London, UK
What kind of work does Tellart do?
Tellart is a design firm that creates experiences that straddle the physical and digital world. We don’t work in any particular industry. We do a lot in the cultural sector for museums and cultural institutions, creating exhibitions and interactive spaces and working on the strategy of their visitor experiences. We also do a lot of work with brands and corporations both on the product innovation side and on the marketing and communications side.
On product innovation, a lot of times we will partner with an internal innovation group at companies like Google, Samsung, Humana, or other large corporations to work with them on the development of next-generation or future-focused products and services.
On the marketing side, we may work directly with brands but also partner with ad agencies such as Wieden + Kennedy.
How does Tellart view the relationship between the digital and the physical?
We view the digital and physical world as the same. When you’re designing an experience, or a product, or a space, some of the touchpoints that people will interact with are going to be physical objects, but those objects may also have some correlated experience online or there may be technology embedded in the objects that you touch. As a design firm, we treat these intangible qualities of an experience — such as software, networks, and interactivity — as a design material alongside wood, metal, glass, and plastic. They’re all intrinsically bound to one another. So, our design process revolves creating the best experience using a wide array of tools.
Often times, traditional craft marries well with new and emerging technologies.
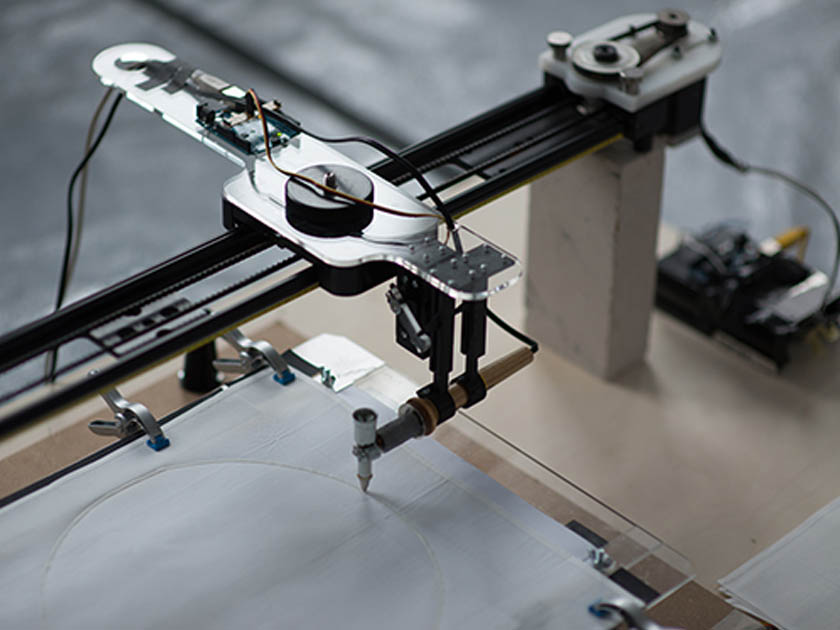
For an installation at Droog, in Amsterdam, Tellart made star maps by printing beeswax onto cotton scarves.

The scarves were then dyed indigo using an old Japanese technique.
How do you use 3D printing?
We use 3D printing as a tool for prototyping and model making. In the case of something like the Museum of the Future exhibition in Dubai, where there are a lot of complicated parts to its interior architecture, we used 3D printing as a tool for mocking up that experience in real space.

The Museum of the Future: Climate Change Reimagined at the 2017 World Government Summit Dubai, UAE
If we are creating a single product, or a physical thing that someone is going to be manipulating as they control an experience, we may create 3D printed versions that allow you to feel that in your hand and determine scale and sizing.
Also, we sometimes use 3D printing for a finished end-product of an experience. For example, right now we are working with a major museum in the U.S. for an experience where we are allowing people to handle 3D printed replicas of certain artifacts that are displayed nearby. We are using a touch table with object recognition to educate people about how those objects were used in their everyday context.
How have you seen 3D printing develop over time as a tool for Tellart’s process?
3D printing is now part of a suite of tools that we rely on as part of our design process. Our design process wouldn’t quite be the same without 3D printing as an option. It depends on what we are doing: Not every project requires the use a 3D printer, and others benefit greatly. Given the expansion of capabilities and materials from companies like Shapeways, I can see it becoming a larger part of projects that we offer.