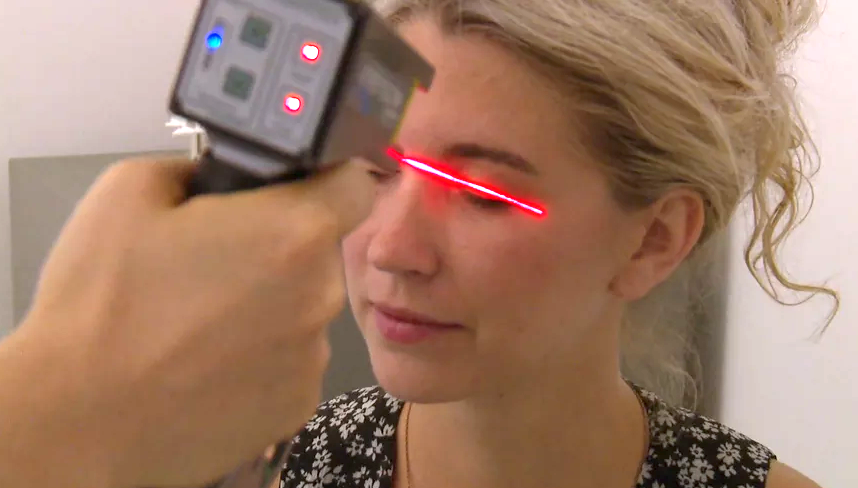
Recently it came to my attention that one of our community members runs a 3D scanning business. As a scanning enthusiast, I had to know more about what she’s doing. So I got in contact with Sophie Barrett-Kahn and asked her the tough questions on 3D scanning and turning 3D scanning into not only art, but also a business.
Emerging Jobs: 3D Scanning Pro from One Planet Pictures on Vimeo.
Sophie runs a studio in New York, called ScannerWorks NY. She has been working with 3d laser scanners and printers since 2003. She has an MFA in Art & Technology studies from the School of the Art Institute of Chicago, and has experience in preparing prints for almost any 3D printing technology that you can think of.
How did you come about starting a business in 3D scanning?
I’m a visual artist and I needed the scanner for my own artwork. I took out a lease on one during art school, and had to come up with the payments somehow! I realized that there must be other artists with the same need. I also know how overwhelming the world of 3D can be if you’re new to technology, as I’ve struggled with it so much myself as an artist, so I started the business to help demystify digital production for people who don’t have that background and just want to get their work made.
What types of things do people ask you to scan? What kind of requests do they have?
I am endlessly surprised by the phone calls I receive. The bread and butter of my business is scaling maquettes for sculptors: I will 3D scan a small piece they’ve made, and then provide a digital file which they can modify, sculpt and fabricate at a much larger scale using CNC milling. But I’ve also scanned surfboards, meditation stools, toy prototypes, train and car parts, furniture, flowers… really, anything handmade or analog that needs to be brought into the digital world so it can be modified and remade. I’ve scanned art and architecture for archiving and historical preservation. I’ve also scanned celebrities, singers and models. More recently, I’ve had people requesting facial scans in order to pre-visualize the results of plastic surgery… There’s never a dull moment!
How do your customers find out about your services? Do you find you need to educate them on what a scan can do for them?
Google ads, word-of-mouth, and a lot of in-person networking. Mostly the people who find me already have an understanding of how 3D scanning can help them, but I also work on educating potential customers. I often receive emails requesting guidance on developing a project, from people who aren’t sure whether digital is the way to go. Sometimes it isn’t – there are cases when a sculptor can achieve the results they want using analog means like mold making and casting. But if they want to scale an object up or down, or modify it in ways that can’t be done by hand, then digital is usually the better choice.
How did you first connect with Shapeways for printing these scans?
I use Shapeways for my own sculptures and have actually been a customer for five years. It’s nice that the pieces are printed here in New York City.
What kind of hardware do you use to scan and how did you come about using it?
I have a Polhemus Cobra handheld laser scanner and a DAVID SLS structured light scanner. I have been using the Polhemus for a long time in my artwork because I love the errors that it generates; when I started doing commercial work I had to learn to use it correctly, which is an entirely different skill set! I have tried quite a few other systems. I use the Polhemus in my artwork, so I would use it regardless. I love the DAVID scanner. The level of detail it can achieve on small objects is really amazing. Results from Sophie scanning of a boot for The Frye Company and a minifig for Lego
What kind of advice would you give others looking to start a 3D scanning business?
For scanning physical objects, location is everything. 90% of my clients are based in Brooklyn or Manhattan, and because the objects I scan are handmade and unique, they either bring me their pieces in person, or have myself or an employee come to their space to scan. Even though the end result is digital, and many of the ZBrush artists I collaborate with work remotely, my role in the process needs to happen here in New York. I also try to connect clients to local fabricators whenever possible. I’m not sure my business model would work in a smaller city with a smaller concentration of creative people; those people would need to be scanning items by mail, and then they would be competing with a larger tier of businesses. I also strive to provide a higher level of service: I bring an artist’s perfectionism to the work I do, which my clients appreciate, and I have experience in 3D printing and casting my own sculpture so I can consult on the entire production workflow, and make referrals to designers and fabricators if my clients need guidance. I liaise with designers and fabricators, and I keep in touch until the job is done, to make sure that the end result turns out the way my clients want. So I would say to concentrate on your local creative networks, and build your business around your own strengths and experience.
What do you see for the future in 3D scanning?
I hope that the software and hardware will become more accessible and user-friendly – even though that may cut into my own profit margins! I’m not too worried; my feeling is that photography is incredibly cheap and accessible now, but people still need professional photographers and photography educators, and I see scanning going the same way. I’d love to scale up and start a Shapeways for 3D scanning, but I’m not sure if the market exists quite yet. As more and more people understand the vast potential that scanning has, I think demand is going to grow exponentially.

What a wealth of knowledge we have in our community! Thank you so much Sophie for allowing me to interview, and sharing such valuable information with us! And thank you for helping us build into an even greater 3D printing community.
This is wonderful!!!! I have been dreaming about 3D printing for a really long time and so happy to see this technology getting more and more accesible to the people….