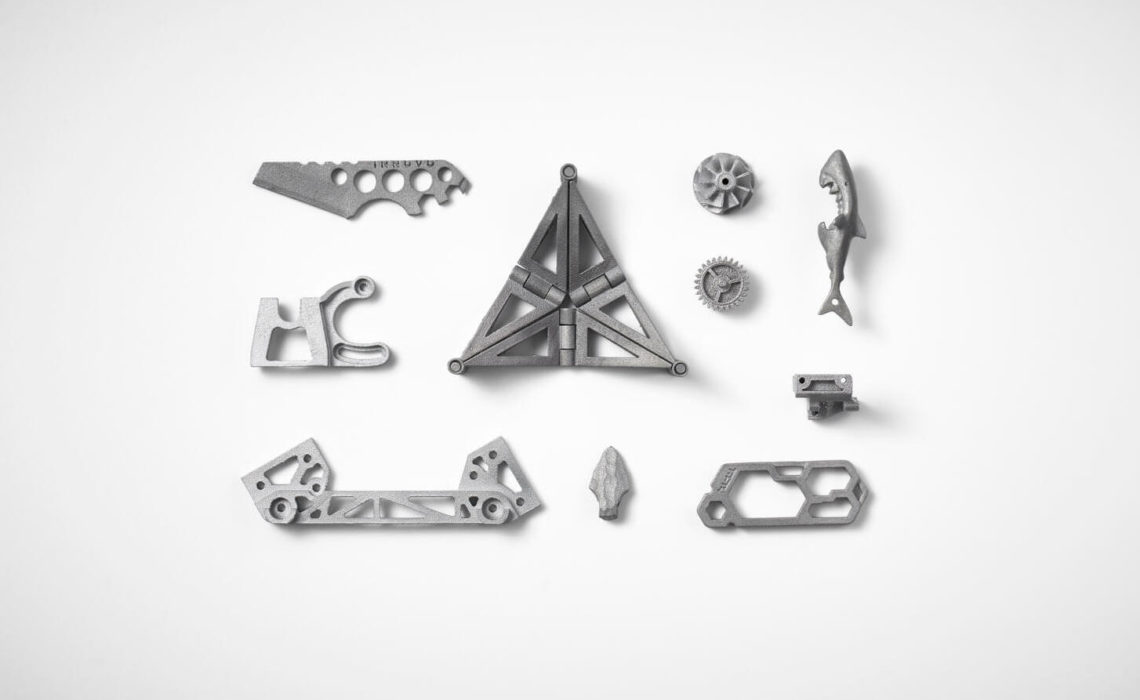
Created to facilitate 3D printing metal powder, Selective Laser Melting (SLM) emerged from a technology lab at the renowned Fraunhofer Institute in Germany. More formally known as Laser Powder Bed Fusion (LPBF), SLM 3D printing relies on powerful lasers to melt metal, whether in its purest form or as an alloy. In comparison to other similar and widely used technologies like Selective Laser Sintering (SLS), the difference is that metal powder is completely melted, providing stronger parts with little potential for voids, or areas where material infill is lacking.
During SLM 3D printing, an incredibly precise laser acts as the impetus for welding metal powder particles together within an enclosed industrial 3D printer. Layer by layer, the powder is melted until the desired structure is complete, with the part anchored to the build plate (along with support structures if there are any) and removed in post processing. At the end of the process, parts and any supports are removed, and the typically rough surface may be further machined.
Selective Laser Melting is is Integral to Metal 3D Printing
As metal 3D printing continues to be more accessible, affordable, and popular among industrial manufacturers, the industry is booming. Recent projections show the international metal 3D printing market reaching $11.6 billion by 2028. This expected growth reflects an increase of 19.5% CAGR from 2022-2028, with 3D printing of functional parts–rather than just rapid prototypes–expected to expand significantly.
“Based on technology, the market is segmented into Selective Laser Melting, Electron Beam Melting, Electron Beam Freeform Fabrication, Laser Metal Deposition, Direct Metal Laser Sintering, Laminated Object Manufacturing, Inlet Printing, and Selective Laser Sintering. The Selective Laser Melting segment acquired the highest revenue share in the metal 3D printing market in 2021.”
“The benefits and ease of operation associated with SLM technology are encouraging its adoption. Additionally, advancements in technology and aggressive research and development activities carried out by industry experts and researchers are opening doors for a variety of other efficient and reliable technologies,” states research by GlobeNewswire.
Metal materials are trending upward in use for 3D printing with Shapeways customers due to the ability to make stronger parts that are lighter in weight. It’s possible to make more complex geometries than before, and supports are not always required, leading to expanded design freedom. Manufacturers can achieve many of the same benefits as traditional manufacturing, compounded by improvements like tensile strength, allowing parts to bear a heavier load.
Typical applications for SLM 3D printing with Shapeways include:
- Aerospace
- Automotive
- Energy
- Machining
- Medical
- Robotics
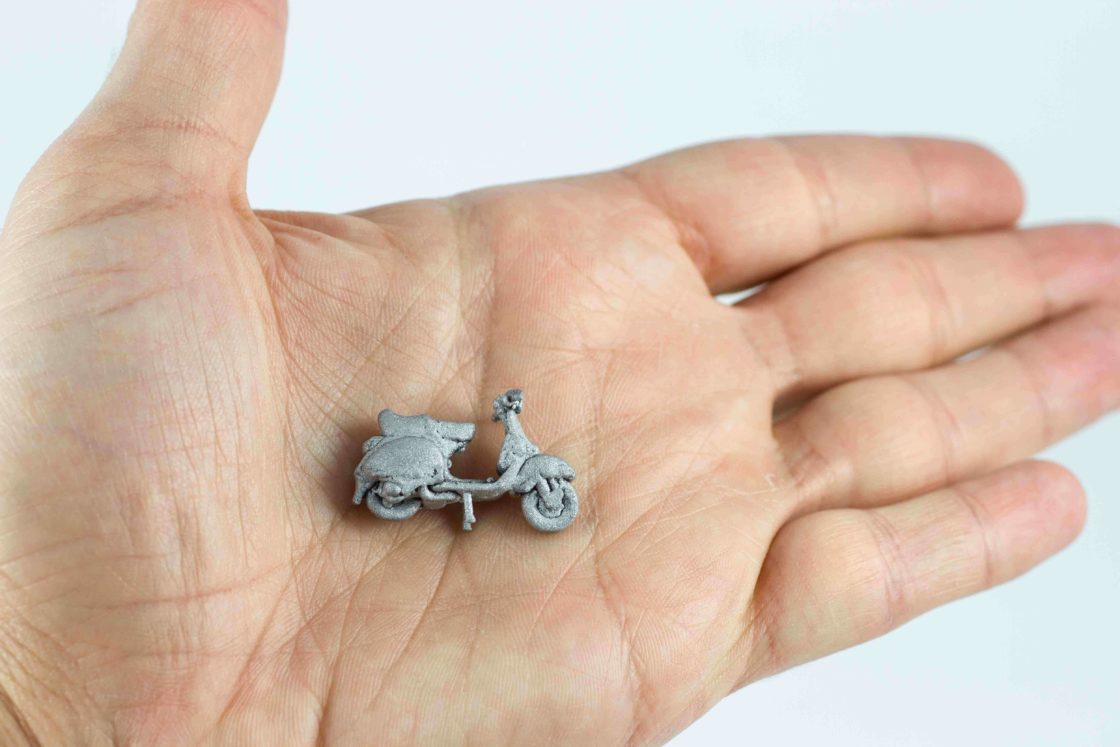
The Benefits of Using SLM 3D Printing
For some manufacturers engaged in production of industrial parts, 3D printing only comes into play when they have exhausted the limitations of traditional methods. While conventional production offers benefits in mass production, SLM offers a host of advantages. Beginning with the ability to engage in direct manufacturing, lead times are shortened or eliminated, and tooling is not required.
Metal additive manufacturing contributes to greater sustainability in production, using less energy with faster production, and less materials as the powder can be reused. In fact, with up to 90% of the powder accounting for build volume in each case, massive amounts of material can be mixed with virgin powder and reused over and over. 3D design is responsible for promoting greater topology optimization. SLM minimizes the use of materials while maximizing production quality.
Greater design freedom is afforded when supports can be avoided. In comparison to other technology like Selective Laser Sintering 3D Printing or Multi Jet Fusion with the use of materials of thermoplastics, SLM parts may require supports. In some cases, the additional stability may be necessary to a strong foundation for building the part layer by layer, affixing it to the build plate, decreasing the potential for warpage, and also promoting better cooling.

From Rapid Prototyping to Mass Customization of Functional Parts
3D printing has changed the face of product development, making it possible for designers, architects, and engineers to create models–and make changes to them–rapidly. Feedback can be elicited as needed, and for Shapeways customers there may be the need for one iteration, a handful of them, or a hundred. It has become much more common for SLM 3D printing customers to go from prototyping to manufacturing end-use parts with Shapeways too.
On-demand 3D printing continues to be a tremendous boon for manufacturers who may watch their inventory gather dust due to unpredictable purchasing patterns. This can be especially true in applications like automotive, where a shop is expected to have most parts in stock. With 3D printing, parts can be kept on a digital file, manufactured as needed, and shipped through Shapeways in customized packaging. 3D printing allows for highly customized runs, often in lower volumes–and costs tend to be lower than creating molds for a smaller number of parts.

SLM 3D Printing with Aluminum
An extremely viable option for metal manufacturing of nearly any kind, Aluminum is used–and recycled–around the world for the fabrication of millions of structures and parts. Aluminum 3D printing continues to trend upward at Shapeways due to the ability to lightweight parts that are intrinsically strong.
Shapeways offers AlSi10Mg for 3D printing with Selective Laser Melting (SLM). A blend of aluminum, silicon, and magnesium, AlSi10Mg is highly suited for parts requiring resistance to corrosion and parts requiring thinner walls. Aluminum is temperature, pressure-resistant, and skin-friendly.
Other benefits include:
- Good strength to mass ratio.
- Low density, which lends itself to lighter weight, strong parts.
- High thermal conductivity, used for 3D printing parts like heat exchangers in engineering applications.
- Very high electrical conductivity, which is useful for parts like wires used in power applications.
Shapeways offers Aluminum in Standard finish only. Find out more about the design guidelines for this metal 3D printing material here.
About Shapeways
Enjoy the benefits of this advanced technology and a wide range of materials from Shapeways for 3D printing your creations with accuracy, complex detail, and no minimum or limits in terms of mass customization or single part orders. Shapeways has worked with over 1 million customers in 160 countries to 3D print over 21 million parts! Read about case studies, find out more about Shapeways additive manufacturing solutions, and get instant quotes here.