We learned of a clever hack to protect 3D printers from… hackers, celebrated a breakthrough in 3D bioprinting, watched the marines add additive to their kits, and saw a Switch controller go one-handed, all this week in 3D printing.
Switch to accessibility
The Nintendo Switch has inspired tons of clever 3D printed mods, mostly focused on making the Joy-Con controller easier to use. But, if so many gamers feel the need to accessorize the Joy-Con for accessibility, what about those with disabilities? Josh Zirl of the AbleGamers Foundation, which helps gamers with disabilities access game play, wrote, “it is disappointing to say the least to see Nintendo ignoring accessibility so completely.” Luckily, engineer Julio Vazquez has created two adapter designs that allow for one-handed game play. As The Verge reported, Vazquez developed the designs after a good friend lost the use of one of his hands — and with it, his ability to play The Legend of Zelda: Breath of the Wild. Now, we just need to 3D print this guy a medal for being such a solid friend.
White hat/black hat
As more and more critical infrastructure comes to rely on 3D printing, security vulnerabilities inherent in any connected device become more of a problem. Think hacking driverless cars to get a sense of how that can play out. The problem with 3D printing is that a hacker could alter a design, affecting its integrity, without anyone realizing it — until a beam comes crashing down in your Mars mansion. As with any threat, however, the best defense is a good offense. Enter a team from Rutgers and Georgia tech, who published the amazing titled peer-reviewed study “See No Evil, Hear No Evil, Feel No Evil, Print No Evil? Malicious Fill Pattern Detection in Additive Manufacturing.” As it turns out, “Just looking at the noise and the extruder’s motion, we can figure out if the print process is following the design or a malicious defect is being introduced,” noted Saman Aliari Zonouz, a co-author of the study. The team came up with three methods: examining the prints carefully (like, CT-scan carefully), tracking the nanoparticle signature of of the print, and, perhaps the simplest, a system of acoustic verification, where the sound of the printing process is recorded for a reference print and tracked against successive prints. Turns out you can learn a lot just by listening.
Mars mansions aside, we’ve already seen what a hacked 3D printed file can do…
Semper Fi, fab-ulously
The U.S. Marines are some of the toughest fighters on earth, and their tools have to be just as tough. So, you might not easily picture a 3D printer embedded in a Marine battalion. But, in places where it can takes weeks or months to replace broken parts, a mobile 3D printing lab could be mission-critical. SpaceDaily reported that the Marine Corps is now testing a mobile 3D printing fab lab, the fabulously acronymed X-FAB (expeditionary fabrication). It’s a 20 x 20 ft. shelter that houses computers and printers in volatile field conditions. Because 3D printing is exactly as badass as we thought it could be.
Get the tissues
We’re all waiting anxiously for the promise of bioprinting to be fulfilled, and we’re now one step closer. Scientists at the University of Oxford have developed a new way of 3D printing living tissue, solving a problem that’s plagued researchers: the movement and collapse of 3D printed cells. By containing the cells in protective nanoliter droplets in a lipid coating, the survival rate of the cells improves, and the tissues hold up. Which organs the tissues become is determined by the stem cells used in the 3D printing process. Now that we have a firmer set of building materials to rely on, we should be able to speed the process of 3D bioprinting the organs that could one day save our lives. And, you know, create new kinds of tasty lab-grown meat.
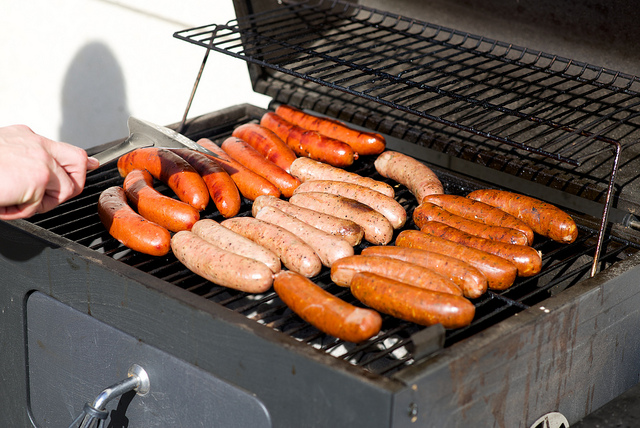
Could the sausage factory of the future be a fab lab? (Photo by Jun Seita CC BY 2.0)