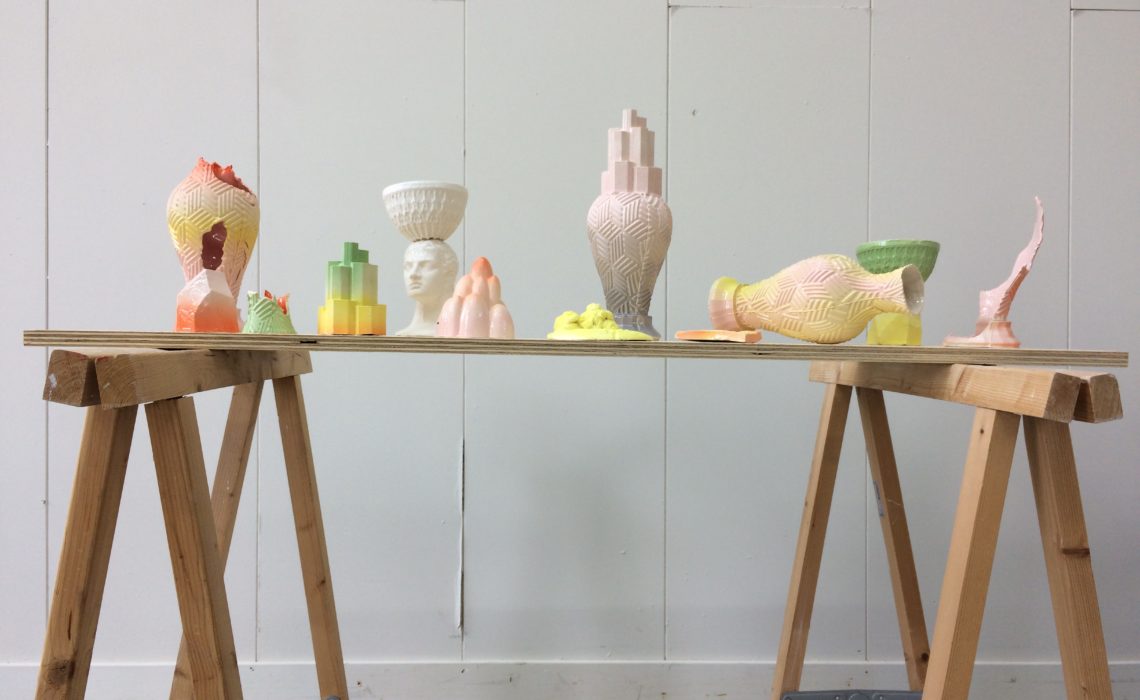
Why powder-based materials continue to be so present in 3D printing
Powder-based methods in 3D printing, generally revolving around technology like selective laser sintering (SLS), are prevalent in manufacturing today, becoming more necessary than ever for powerful applications requiring performance and safety. Modern designers and engineers rely on plastic powders, metal powders, and a range of impressive techniques to fabricate robust tools and critical parts for important industries like aerospace and the automotive industry. And although organizations like NASA and a handful of car manufacturers may have known about (and have been using) 3D printing since its inception, the secret is certainly out—after decades under wraps.
Although resin and powder-based technology both tend to offer better accuracy and precision in the finished 3D printed product, with SLS, supports are not required as unsintered powder surrounding the parts acts as a convenient support system during the process. Eliminating supports also offers enormous advantage for users who may have already done their time trying to bolster overhangs and bridges, wasting extra material, creating more work in the end, and possibly opening up parts to vulnerability in terms of scratching or harm during post-processing. Without added effort expended in removing supports, users can turn their attention to valuable processes like testing prototypes and new parts. More complex parts can be easily created too, to include connecting and moving parts.
Materials for 3D printed molds may be made from nylon, plastic, metal, or even sand
Users are generally interested in fabricating molds so that they can make multiple copies of one object or a part. The 3D printed mold acts as a vehicle for liquid which then hardens inside during the casting process, resulting in the desired structure (also referred to as the casting, making the terminology a bit confusing).
While durable nylons like the Shapeways’ Versatile Plastic (also known as Nylon 12 plastic or PA12) are suitable for making jewelry and technical accessories, industrial users also rely on them to make a wide range of mechanical parts, fixtures, cases—and in the medical field, even prosthetic devices for amputees in need of limb replacements. Versatile plastic can also be used to create sturdy molds for SLS 3D printing, along with Thermoplastic Polyurethane (TPU), which is often viewed as a good substitute for silicone in molds, due to its extreme flexibility. MJF Plastic PA12, another material well-suited for applications such as mechanical parts, cases, drones, and prosthetics, can also be used via Multi Jet Fusion technology for creating master patterns leading to casting.
Users may employ sandstone for 3D printed molds in some cases too, although it is more brittle and requires very careful handling. There could also be serious questions over what is used for casting, as filling a sandstone mold with hot metal would most likely cause it to degrade quickly, and intensely. (Sandstone is also used in other industrial applications such as eyeglass frames, mechanical parts, drones, and again—even prosthetics.)
Metal 3D printing is one of the hottest technologies in manufacturing today, especially as industrial users can look forward to the opportunity for building stronger parts that are lighter in weight. For casting though, metal powders (stainless steel, steel) are used to create a variety of helpful molds (as well as the castings themselves), from assisting in jewelry making, to stealing away some of the tasks typically relegated to foundries.
3D Printed Molds Are Disrupting Traditional Methods as Old as the Middle Ages
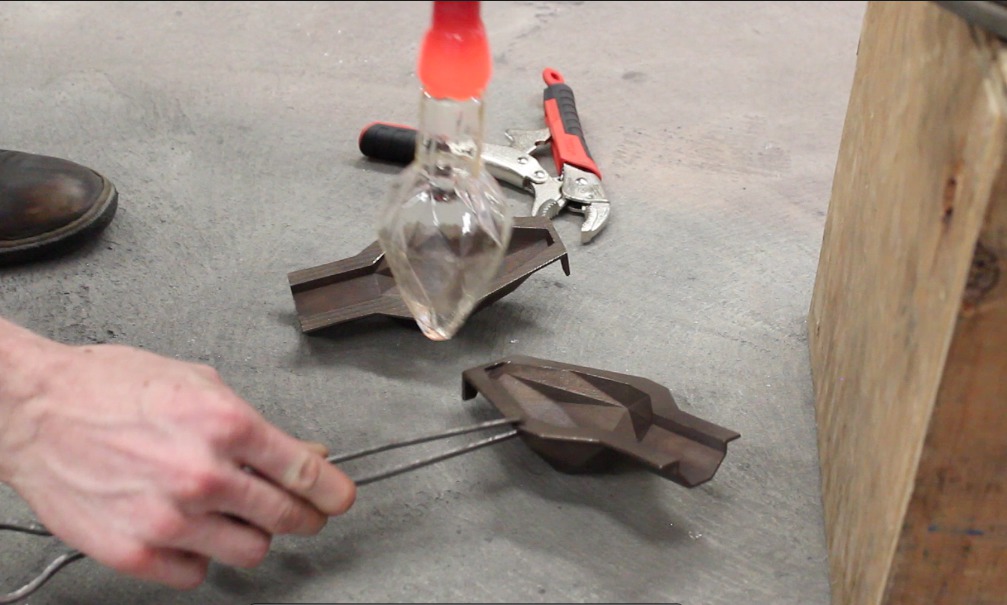
Traditionally engaged in the process of making molds and casting, foundries are factories dedicated to casting molten metal which is then solidified into the specific parts requested by customers. These types of establishments have been around since the 1400s formally—but traditional casting methods are thought to go back as long as 5,000 years ago for production of a variety of substantial metal products to include ammunition.
As 3D printing has swept through the mainstream and maintained a strong presence over the last decade especially, traditional businesses like foundries have been forced to give up at least some of their profits to the additive manufacturing industry. Again, the ability to print without supports makes a huge difference, as well as being able to print multiple parts in one run. 3D printing is often referred to as the fourth industrial revolution due to a long list of benefits outweighing traditional manufacturing—from greater affordability in the long run to better speed in turnaround for customers, the ability to make obsolete parts, lightweight parts, and in many cases—parts that could never have been created at all with traditional technology.
It might be hard to imagine that such a long-lasting trade could suddenly begin to disappear, but time will tell in terms of consumer demand from the industrial level. Industrial metal 3D printers are very costly though, and may be the saving grace for foundries worried about going out of business due to an upstart like progressive digital fabrication.
Just the fact that a 3D printing enthusiast could fabricate, test, and use functional molds on their own (and create their own mini-production line) speaks volumes for the technology. The unprecedented independence allowed in creation and subsequent production, as well as providing a ripe scenario for innovation like the world has never seen before continues to make 3D printing enticing to the public. Disruption is also a major factor, and perfectly demonstrated here as the normal balance for foundries is being rocked more and more with 3D printing garnering interest worldwide, and moving in on age-old production systems.
Casting with 3D printing means better speed, and improved savings on the bottom line
No matter what your 3D printing level of expertise is so far, it is important to understand what materials are available to you, and why they are used in different techniques. From the desktop realm, and large-format industrial manufacturing too, fused deposition modeling (FDM) is now the most ubiquitous technique, accompanied by a massive—and ever-expanding—industry centered around sales of thermoplastic filaments (mainly in the US). Still though, FDM is often forced to take a back seat in comparison to the more classic forms of 3D printing, invented decades ago for rapid prototyping in engineering.
Powder-based technologies differ from extrusion vastly. Created back in the 80s by Dr. Carl Deckard and Dr. Joe Beaman at the University of Texas at Austin, Selective Laser Sintering (SLS) 3D printing binds powder particles together with a laser. This occurs after the 3D model is designed and then sliced, creating the layers to be deposited until the structure is complete. Metal, plastic, ceramics, and other types of powder can be used to create castings for prototypes, along with low-volume batch production of functional parts. Other powder-based technologies like binder jetting are expected to continue on as a highly sustainable production method due to the incredible speed at which they work, producing large volumes of parts.
From prototyping to the manufacturing of products that are not only functional, but high-performing, the evolution of FDM 3D printing and continued popularity is undeniable; however, the heavy hitters, the originals, the formative technologies like selective laser sintering (SLS) and stereolithography (SLA) continue to perform solidly within additive manufacturing, and are relied on for higher quality prototypes and end use parts resulting in better form and accuracy. While these technologies may have some desktop 3D printing counterparts, overall, industrial users rely on them with industrial hardware and software to manufacture complex parts that will stand the test of time, whether in terms of everyday tools or rocket parts.
No matter what type of technology you use, learning to use molding processes properly could benefit you greatly in the future. Such knowledge offers a valuable skill set, whether you are using your learning on the job or for your own projects. While we are all aware of the intrinsic, revolutionary benefits of 3D printing in terms of the ability to customize and make on-demand products, molds allow you to create a veritable low-volume factory setting where parts are replicated identically each time. This ability offers significant advantage to a business of any size, allowing them to design parts, print molds, cast, and perform manufacturing duties without having to wait on or pay a middleman. 3D printing molds can be a great way to reserve capital in terms of production too, although investment in technology may be of concern.
Direct Casting Leads to Faster Mass Production of Your Product
In casting, the requirements are simple, as there must be a 3D model and then a mold which is made up of the product features in negative detail. Using investment casting in 3D printing (also traditionally known as lost wax casting as hot metal introduced to the mold melts the wax insert), metal patterns can be directly fabricated—embracing some of the most classic benefits of 3D printing in savings of time, while also greater latitude in design to create complex shapes to include cavities and other intricate details. The cooling process is more stable, and objects like tools are expected to be more durable and last longer.
Direct casting works well for large parts or those that could be challenging to work with in wax—considered an indirect molding process due to the numerous steps involved. It is, however, as easy as choosing a material to 3D print in the shape of a design pattern for the mold (to contain liquid casting material), filling it, letting it settle, and then removing the object from within. The hardest part is perfecting your design. Once you complete that step though, each casting is an exact replication of the previous one.
Seeking Resources for 3D Printing? Shapeways Can Help
3D printing allows you to create molds quickly, and also to make changes as needed. The investment is minimal, and the potential is compelling. For high quality castings, it is critical that you understand the process of designing a mold—as well as preparing for how it will pull open so that the structure is not damaged or difficult to remove. And because the capital required to produce industrial-quality molds could put you out of business before you even start, consider using a service like Shapeways to 3D print molds for you—or any other parts or prototypes.
3D printing services from Shapeways such as SLS allow you to reap the rewards of high-performance, quality materials without having to invest all your business capital in the powerful hardware, software, and materials required for your build.