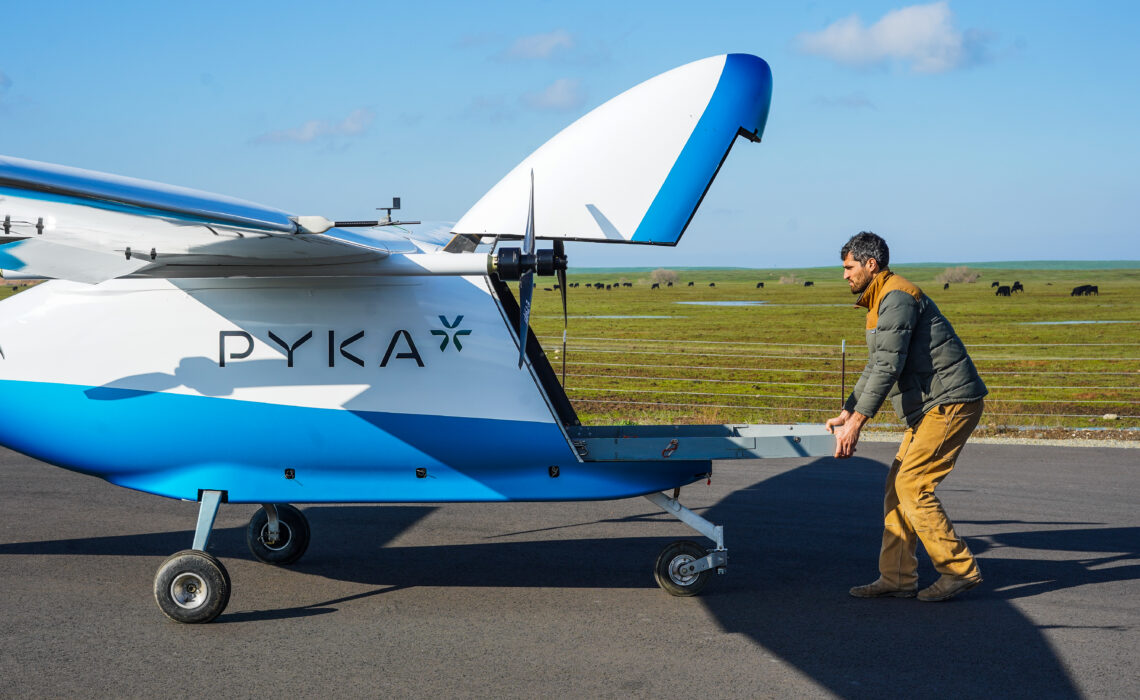
Sleek, fast, and fully-automated. Pyka’s signature electric aircraft are transforming the future of cargo transportation with faster deliveries, improved safety, and efficiency–from ease in taking off to flying in harsh weather conditions.
The expanding product line of the California-based aviation company continues to showcase their impressive vision and versatility, fueled by 3D printing. After mastering design and production of autonomous aircraft for agricultural applications like crop-spraying, Pyka transitioned into developing new solutions for middle-mile cargo transport.
Market Demand Required Modifications to Original Pyka Aircraft Designs
Pyka had great success in producing their first electric airplane, the Pelican Spray, and working in other aerial applications. They quickly piqued the interest of cargo-transport companies.
“Market leaders thought our technology would be perfectly suited for what they needed in moving cargo,” said Jason Petersen, Senior Mechanical Design Engineer at Pyka. “Supply chain influenced that a bit, but overall, the aviation industry was primed to advance and our electronic aviation technology was the most sophisticated.”

Meeting the needs of new clients meant making changes to existing technology. Pyka spent a year modifying and creating new aircraft that could fly longer distances, hold more cargo, and would also be easy to maintain.
3D Printing Accelerated Product Development & Manufacturing
3D printing played a large role in streamlining those modifications, and has continued to accelerate Pyka’s production development and manufacturing processes. “People are often surprised at how often we use 3D printing in our aircraft,” said Petersen.

While there are dozens of 3D printed parts on each aircraft, some examples include waterproofed fairings, cases for wires and smaller electronics, latch mounts, and user-interface panels. Pyka reports ease in designing around any problems, without ever having to worry about ‘manufacturability’ of parts in 3D printing.
“Design freedom plays a large role in allowing us to prototype and make changes, strategically placing certain materials where we know added strength is necessary in the aircraft’s geometry,” said Petersen. “With 3D printing, we can create much lighter parts for complex structures, in comparison to injection molding or machining.”
Affordability in prototyping and production is a major advantage as the Pyka team is constantly testing parts and looking for ways to enhance their products, usually revising at least one 3D printed prototype per week. Their design team uploads 3D models to Shapeways quickly, receives instant quotes and printability analysis, and then also has the advantage of referring back to those same digital files for on-demand additive manufacturing.
Advanced 3D Printing Thermoplastics Meet Pyka’s Growing Needs
The autonomous aircraft designers leverage technology like Selective Laser Sintering and Multi Jet Fusion because of the ease in redesigning parts, and maintaining them later. Materials like Nylon 12 [Versatile Plastic] make it possible to create durable yet flexible parts, while MJF Plastic PA12 provides necessary properties like moisture- and chemical-resistance.
“We’ve experimented with metal 3D printing and other materials like Polypropylene, but I find we always end up going back to the other materials because of their excellent strength properties. We’re used to working with them, the outcome is predictable, and the price point is just hard to beat!” said Petersen.

Access to advanced, durable materials is critical because Pyka uses so many of the 3D printed parts to hold important aircraft components in place–when installing a part requiring complete accuracy on top of a wing, for example–or on a curved area of the aircraft.
Currently, the average Pyka aircraft includes 60-80 3D printed parts. The company’s rapid expansion in agriculture and cargo transport is fueled by their ability to simplify design and production with additive manufacturing, resulting in 11 aircraft built and 45 more planned for deployment in the future.