
Metal materials continue to be in high demand for 3D printing, with this area of the industry growing at an accelerated pace. Used in many leading industrial applications, metal 3D printing is relied on by large aerospace organizations and manufacturers like automotive companies because of speed in production and strength in materials.
3D Printing Steel with Binder Jetting
As metal 3D printing matures, Binder Jetting is a popular technology for manufacturing high-performance parts—and is predominantly used by Shapeways manufacturing partner, ExOne. In line with the Shapeways ongoing dedication to sourcing other third-party materials too, it is important to note that ExOne, founded in 1995, also has extensive experience in 3D printing with materials like ceramic and even sand.
“Around the same time we started working with Shapeways, we also transitioned into using stainless steel,” said Brandon Cary, Technical Sales Manager at ExOne. “There’s a lot of focus on automotive, and we touch a lot on the industrial markets like aerospace, and defense too. We are transitioning heavily into medical as well today, and have always been very successful in architecture, as well as consumer-based lines, along with areas like jewelry too.”
“The direct metal business is aggressively growing as additive manufacturing grows in the world.”
ExOne Metal 3D Printers
For metal 3D printed parts from Shapeways, binder jetting is performed with the M-Flex and X1 25Pro, both of which are capable of printing with metal powder. An adhesive, or binding agent, re-coats and saturates the build plate of the printer, layer by layer, building the solid 3D printed structure.
Metal 3D printed parts are cured, and then de-powdered in post-processing. Afterward, parts are put through a thermal, sintering operation. Variables are present dependent on the material; for example, in using Steel, there is less shrinkage due to the combination with bronze. Support materials are not required during printing with either of the metal 3D printers, because surrounding powder acts as a stabilizing force. Supports may be needed during the sintering process though, with materials like aluminum grit.

Sustainability and Efficiency in Production
A large percentage of the metal powder is recycled, adding considerable sustainability to the process. The 3D printed metal parts only make up seven to ten percent of each build, meaning that all the remaining powder can be sifted and reintroduced with virgin powder. Binders are recycled during 3D printing with metal in binder jetting too.
Both the M-Flex and X1 25Pro are used to 3D print metal powders, but the M-Flex is equipped with an ACT system for advanced compaction in printing fine powders down to 15 micron powders, while the X1 25Pro prints down to 5 microns and is also part of a beta program for Stainless Steel 316L—currently being 3D printed mainly on the M-Flex.
“Detail on a component is driven by the powder size itself and layer thickness,” said Cary. “The finer the layer, the finer the powder, the finer the end resolution can be. The powder is responsible for your end density, material properties, resolution, and everything.”
Benefits of binder jetting include:
- High-volume printing at high speeds
- Design freedom due to fewer limitation in production
- Substantially reduced material waste
- Flexibility in 3D printing with different types of materials
Steel offers high resolution, high wear resistance, increased longevity for products, and over seven finishes are available. With the single alloy, very dense, strong parts with complex geometries can be printed—along with extremely fine, strong features.
Popular applications for 3D printing with steel include:
- Medical devices
- Branding irons and burners
- Automobile parts for restoration of older vehicles
- Tooling
- Fixtures
- Jewelry
One of the critical issues in metal 3D printing that drives design considerations is wall thickness. Minimum wall thicknesses should be adhered to because thin walls have a good chance of causing distortion on the back end of the manufacturing process.
Font and detail are another consideration for designers too. Text, numbers, and details need to have a minimum wall thickness of 0.8 mm to make sure that all of the text appears on the part and isn’t washed out during 3D printing. Considerations must be made for depowdering too, in terms of interior holes and cavities. Inside corners and sharp intersections should have ‘filleted edges,’ along with sharp edges—rounding the insides of the corners.
“We love seeing new designs brought on by customers, and we encourage them to keep pushing and keep thinking outside the box every day,” said Cary.
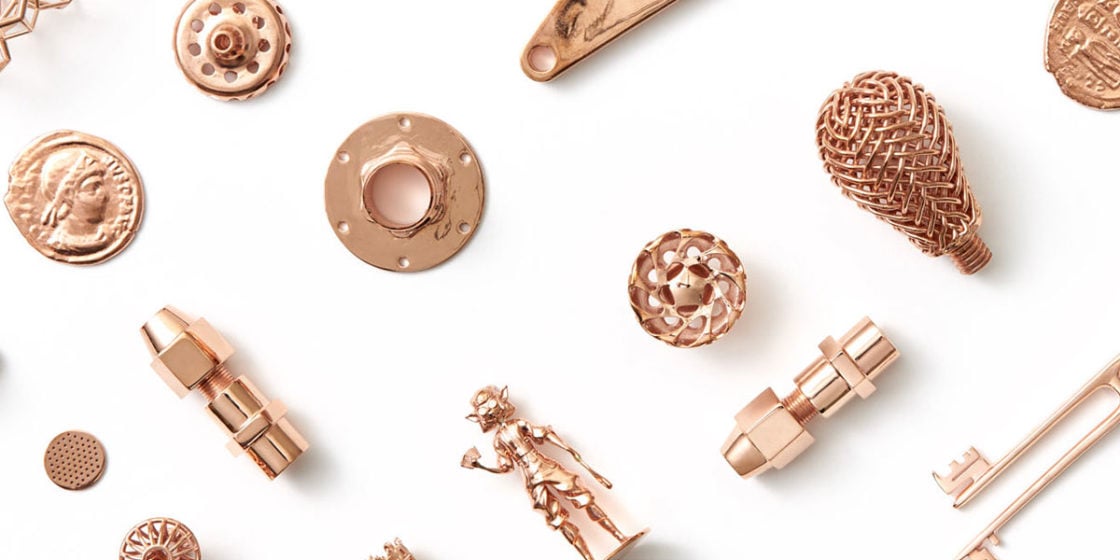
Metal materials available from Shapeways
Stainless Steel 316L – A single alloy made of 100% stainless steel, this material is an industrial metal that can be used for 3D printing products like mechanical machinery or surgical tooling. Resistant to both extremes in low and high temperatures, Stainless Steel 316L is also highly corrosion resistant. Read more about the design guidelines here.
Steel – This material is combined with bronze to create a material that is 60% steel and 40% bronze. Color ranges from silver gray to reddish bronze. Read more about the design guidelines here.
Other types of metal with 3D printing from Shapeways include:
Aluminum – 3D printed with Selective Laser Melting, Aluminum is recommended for outdoor applications due to its corrosion resistance and high electrical and thermal conductivity. This material is designated for end-use parts that must be strong, highly accurate, and low in weight.
Gold, Silver, Platinum, Copper and other precious metals – 3D printed molds are created for metal casting with high quality materials for applications like jewelry, and the Groen and Boothman case study serves as a great example, highlighting their Elements sterling silver bracelet series. Materials like Copper are even more versatile in wax casting, used to make marine accessories, mechanical devices like heat exchanges, home decor, and prototypes.
Read further about all the materials and technology available from Shapeways here.
Contact Shapeways Now
Speak with our Sales Department to find out more about which metal material best suits your needs, and then move forward to enjoy the benefits of 3D printing without having to spend precious business capital on machines and inventories of material. Ready to print? Upload a model now.
Shapeways has worked with over 1 million customers in 160 countries to make over 20 million parts! Read about case studies, find out more about Shapeways solutions, and get instant quotes here.