
Read on to learn about:
- How PA6MF is unique in terms of strength as a 3D printing material.
- Why this industrial material is so popular for engineering applications.
- The power of Selective Laser Sintering technology in combination with PA6MF.
- The advantages of low-volume production and on-demand 3D printing at Shapeways.
Nylon 6 Mineral Filled, Ultrasint® (PA6MF) is an undeniably unique and powerful 3D printing material that Shapeways offers for high-performance parts and prototypes requiring strong mechanical properties. Reinforced with polymer particles, PA6MF provides adaptability and accuracy for quality 3D printing of parts which often possess complex geometries.
The Real Advantage: PA6MF for Small Production Runs
As an industrial-grade 3D printing material, PA6MF continues to be extremely appealing to many manufacturers because it offers properties similar to parts created with injection molding.
“PA6 is essentially one of the most commonly used materials on the planet in traditional manufacturing,” says Steve Weart, Director of Customer Success at Shapeways. “By enabling our customer base to create end-use products with this material through additive, we can provide the ideal solution for low- to mid-volume production requirements for many of our customers throughout the product life cycle.”
While PA6MF is an excellent option for prototyping, Shapeways takes it one step further in offering this material as an excellent alternative for end-use parts. The benefits become even more clear for companies focused on creating highly customized designs for low-volume production. There’s no reason to worry about the complexities of mass production or making molds when 3D printing can do the job quickly, efficiently, and more affordably. Not only that, the ability to make changes quickly in 3D adds a serious advantage to the development and production process–again, saving time and expense; in fact, some customers may make over a hundred iterations in bringing a functional part to perfection.
PA6MF is a good choice for parts that require high stiffness, strength, and heat stability. While all Ultrasint® PA6 materials combine high modulus, high strength, and excellent thermal distortion stability, PA6MF offers added reinforcement with minerals embedded in the powder particles. This promotes better homogeneity in the material, along with improved potential for spreading during the 3D printing process–and recycling after.
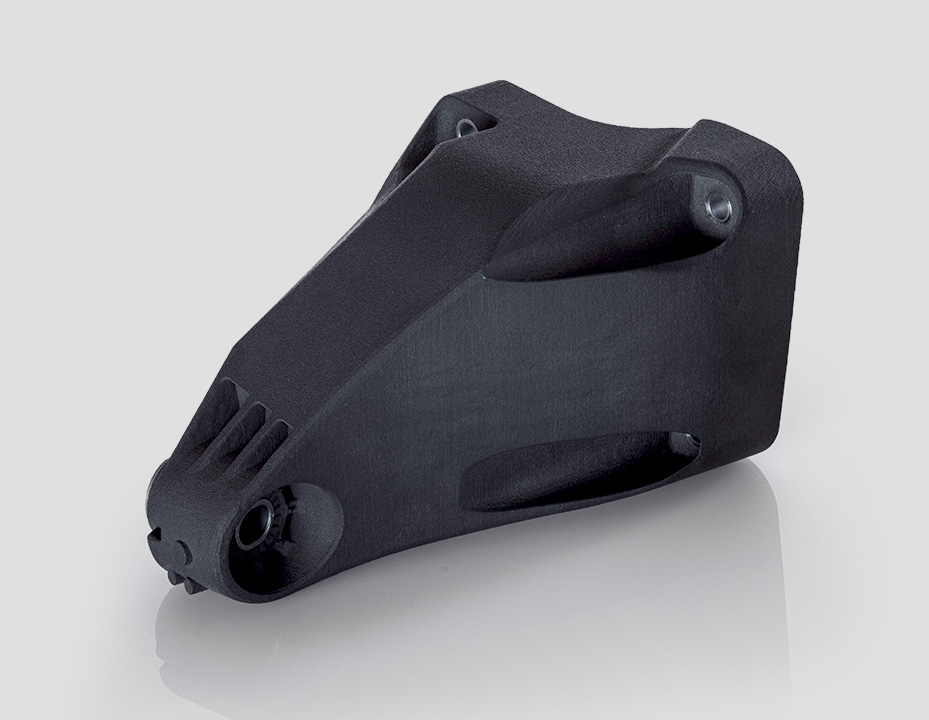
Selective Laser Sintering (SLS) – How the Technology Works
SLS reigns not only as one of the earlier forms of 3D printing, but also still as one of the most powerful and respected methods–even over the original technology known as Stereolithography (SLA), and popular methods too like fused deposition modeling (FDM). This powder-based technology is used to manufacture a host of complex structures that are often not possible with conventional methods, including products with moving or interlocking parts too.
SLS 3D printing begins with distribution of the powder over the print bed, with a computer-controlled CO2 laser tracing the cross-section of the 3D design on the powder. It then scans each layer, fusing them all together at a high temperature (just under the melting point) until the 3D printed structure is complete. SLS 3D printers may range in volume size from 200 mm x 250 mm x 330 mm to 700 mm x 380 mm x 580 mm, with a layer thickness of 100 to 120 microns.
Thousands of parts can be printed in one build, made possible due to the ability to ‘nest,’ by strategically placing parts together in each build. This is also due to another advantage: no supports are required, as the extra powder in each print surrounds and bolsters the desired structures during production. Powder can be reused later too, allowing Shapeways to continue manufacturing with sustainability and lessening the impact on the environment.
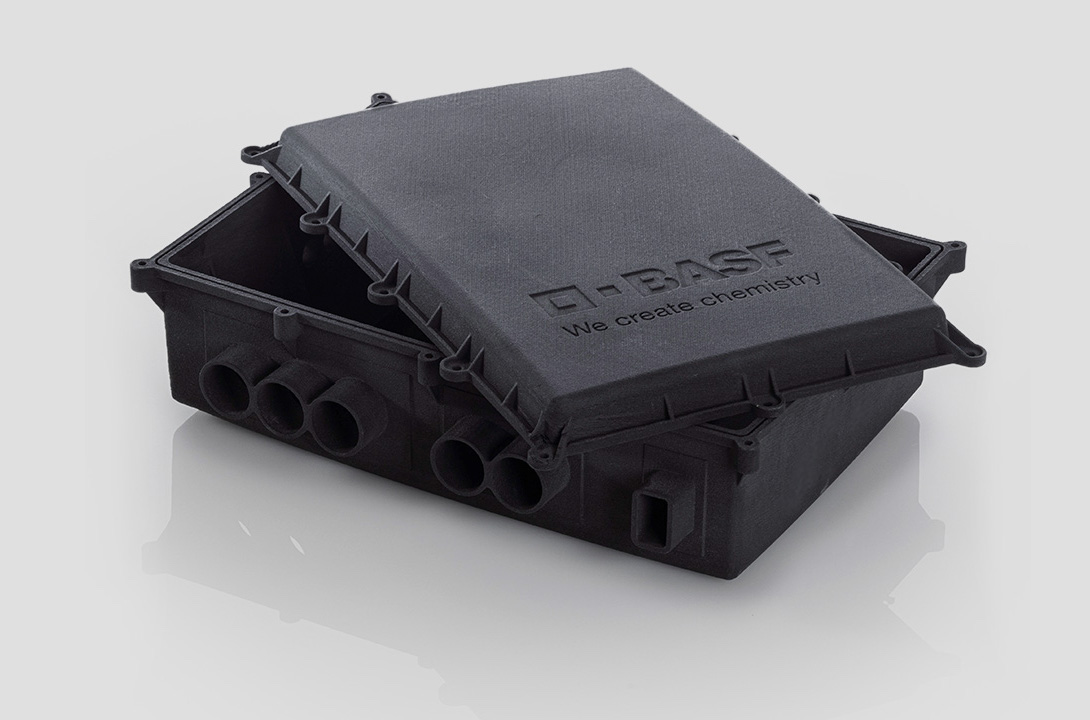
Industrial Background on PA6MF
BASF produces PA6MF under the iForward AM corporate brand. Due to a long-term manufacturing partnership, Shapeways has access to the full spectrum of BASF’s extensive portfolio of resources–providing superior materials designed to meet the highest in customer requirements for 3D printing. Materials like PA6MF play an important role in modern manufacturing as businesses of all sizes begin to explore new ways to improve production, including new hardware, software, materials, and processes like on-demand 3D printing.
Also known as Polyamide 6, Nylon 6, or polycaprolactam, PA6MF is a well-known thermoplastic for engineering applications. It’s common for the focus to be on lighter weight materials–specifically PA11 or PA12–where such requirements are critical to applications like robotics and drone technology. Materials like PA6MF, however, are typically used with strength in mind, for mechanical devices like bearings and structural applications.
Along with its high melting point, PA6MF is also known for:
- Abrasion resistance
- Chemical resistance
- Fatigue endurance
- Good rigidity
- Toughness, and strength against impact
Parts printed from Ultrasint® PA6 MF are naturally black, with a standard matte finish that has a slightly rough surface.
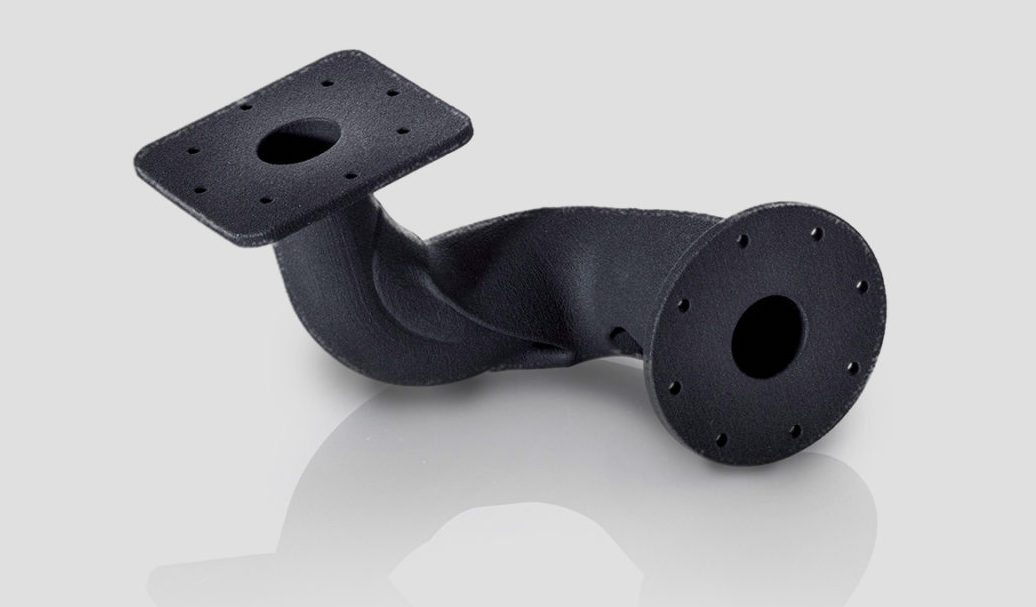
Bounding box requirements are as follows:
Bounding Box Minimum
X + Y + Z > 10 mm
Bounding Box Maximum
375 x 375 x 440 mm
Companies that are new to additive manufacturing may wonder whether or not 3D printed industrial parts will be as good as those made traditionally. The answer is yes. Not only that, these 3D printed parts have the same level of structural integrity.
In low-volume production, 3D printing with PA6MF pays off due to the ability to make a small number of parts quickly and economically, with exact repeatability for every part, every single time.
About Shapeways
Contact Shapeways now to enjoy the benefits of advanced technology and materials for manufacturing creations with accuracy, complex detail, and no minimum or limits in terms of mass customization or single part orders. Shapeways has worked with over 1 million customers in 160 countries to make over 21 million parts! Read about case studies, find out more about Shapeways solutions, and get instant quotes here.