
Developed in a small lab in the 80s, 3D printing originated out of the need to speed up product development. As the decades passed, however, 3D printing evolved from a sophisticated tool for rapid prototyping into one capable of making impressive, functional parts. The technology has not superseded traditional processes like injection molding, but is steadily becoming a more visible partner in the manufacturing toolbox whether for low volume or mass production. Read on to find out:
- Why manufacturers have relied on injection molding for so long but are turning their interest toward offering 3D printing too.
- What’s involved in the decision making process, whether to choose 3D printing or injection molding.
- The pros and cons of each technology, and why it is often important to narrow down decisions case by case.
- Why strategy in scaling is so important for any type of manufacturing.
The decision making process may depend on a traditional manufacturer exploring 3D printing services like Shapeways in order to make new offerings available to their customer base, or a dedicated 3D printing enthusiast may be dealing with larger volumes in terms of orders and wondering if they should make the move to injection molding.
Scaling successfully is key in manufacturing, and business, today, but it can be challenging when growing from 1 to 1,000 units, 10,000 units, or even 100,000 in the luckiest of scenarios. There are many factors to consider when scaling production, but one of the most obvious concerns is how to actually go about creating a product. There are usually requirements for controlling expenses, providing fast turnaround times, and dealing with all aspects of customer service as efficiently as possible too.

Looking Deeper into Additive Manufacturing and Injection Molding
Unfortunately, there is no single manufacturing method that is perfect for every part and situation, but it is critical to understand the advantages and disadvantages associated with methods like 3D printing and injection molding.
When focusing on plastic components and products, there are traditionally few manufacturing methods available, the oldest and most common being injection molding. While injection molding has dominated the manufacturing landscape for decades, newer techniques like 3D printing, have begun to gain traction by offering an alternative, as well as advantages over traditional methods; for example, a company may go straight to injection molding to manufacture plastic products in a high volume of 10,000 parts or more–or they may choose 3D printing for greater flexibility in making designs, multiple iterations, and the ability to make complex geometries not possible before.

Injection Molding
Injection molding is one of the oldest high-volume manufacturing processes, wherein a molten material (such as a thermoplastic) is injected into a metal mold. Once injected, the thermoplastic takes on the mold cavity’s shape, is cooled, and is ejected as a solid part.
Injection molding is typically used for producing high volumes of the same object. The method does have its pitfalls though. First, there is a large upfront investment involved in making a mold. Molds can be reused to make hundreds of thousands, if not millions of parts, but can cost anywhere from a few thousand dollars to over $100,000. As a result, there is an inflexibility that comes with needing to create a new mold for every new or modified part. Still, injection molding is a complex but powerful process that has been the go-to solution in the plastic part manufacturing market for years.
3D Printing
3D printing is also referred to as additive manufacturing–in stark contrast to subtractive manufacturing–as the process involves adding material together to create the end part. This is opposed to cutting material away, like in milling, or reshaping it in injection molding.
There are many benefits inherent to this process, such as the ability to produce completely custom parts with virtually no upfront cost. With 3D printing, the efficiency is incredible: all you need is a digital file. Due to the additive nature, less material is used, and for technology like selective laser sintering, much of the powder can be recycled.
3D printing does have some disadvantages though too, especially as some 3D printing processes are still prohibitively expensive, slow, and may produce parts that are not up to industry quality or material standards. Because it can be difficult to decide between the two, and somewhat complicated, considerations are usually case-specific.
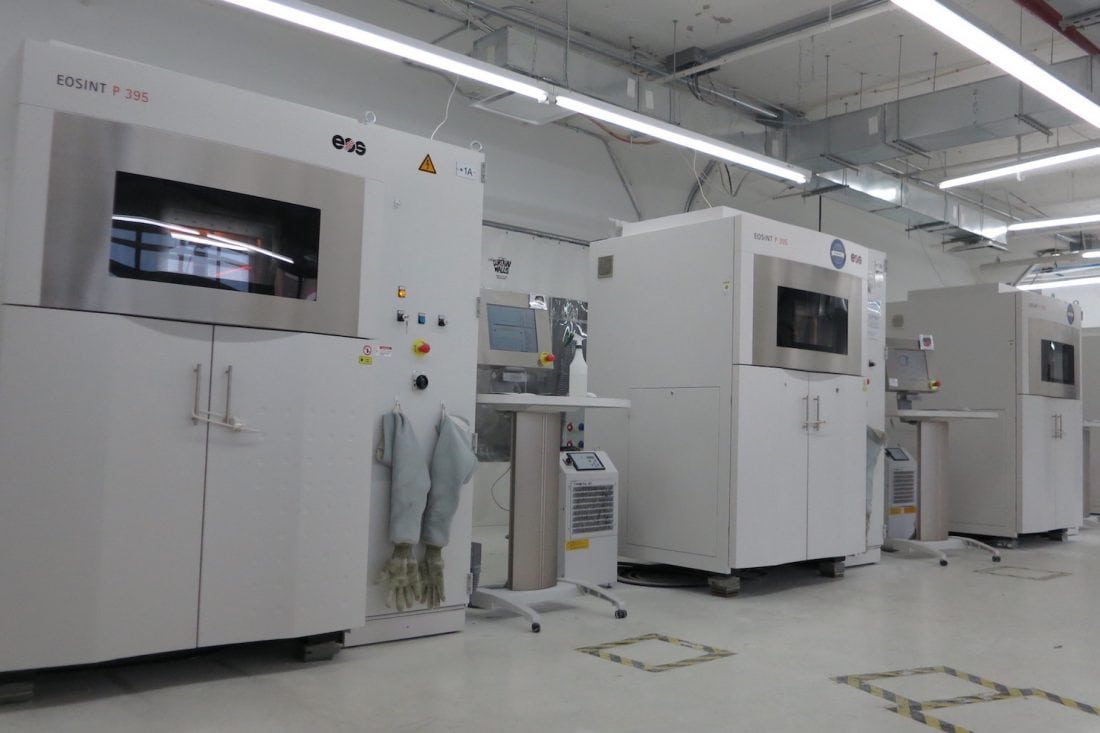
Examine Specific Parts and Production Requirements
Aside from unit cost and order volume, there are other considerations that come into play when choosing between injection molding and 3D printing:
- Complexity – Whether an object is organically shaped or has ultra-sharp edges, its type and degree of complexity can help inform which manufacturing method is best. Ultimately, common sense usually dictates using the most suitable form of manufacturing. When thinking of ‘creative’ or organic shapes as complexity, 3D printing wins. When thinking of hard engineering constraints and tolerances, injection molding wins most often.
- Production Time – Production time is typically determined by the manufacturer’s capacity and the size of the production run. The many steps required to get something into production can factor into this timeline, from sourcing a manufacturer, to making a mold, to quality control, shipping and eventual delivery. Other factors include the manufacturer’s location, steps to getting to production, and guaranteed delivery time.
- Iteration & Change – As with all competitive products and services, being able to iterate often and maintain agility is key to innovation. For businesses at the beginning of a long product development journey, spending a few thousand dollars on a mold that cannot be changed will most likely slow down the innovation cycle; however, if the focus is intense mass production without much worry for customization, then injection molding may prove to be more fitting over 3D printing.
Manufacturing Tools for the Future
The future looks exciting for 3D printing, injection molding, and manufacturing overall. These advancements are making it easier and faster to get things made, and will hopefully lower the barrier so that more and more people can make the products they dream up.
To get the perfect look and feel for any 3D printed part, check out the material options that Shapeways offers. Each material listed notes the available finishing options to ensure that your aesthetic parts look good, and your functional parts perform how you need them to in the end.
Upload your design and get an instant quote now!
About Shapeways
Enjoy the benefits of this advanced technology and a wide range of materials from Shapeways for 3D printing your creations with accuracy, complex detail, and no minimum or limits in terms of mass customization or single part orders. Shapeways has worked with over 1 million customers in 160 countries to 3D print over 21 million parts! Read about case studies, find out more about Shapeways solutions, and get instant quotes here.