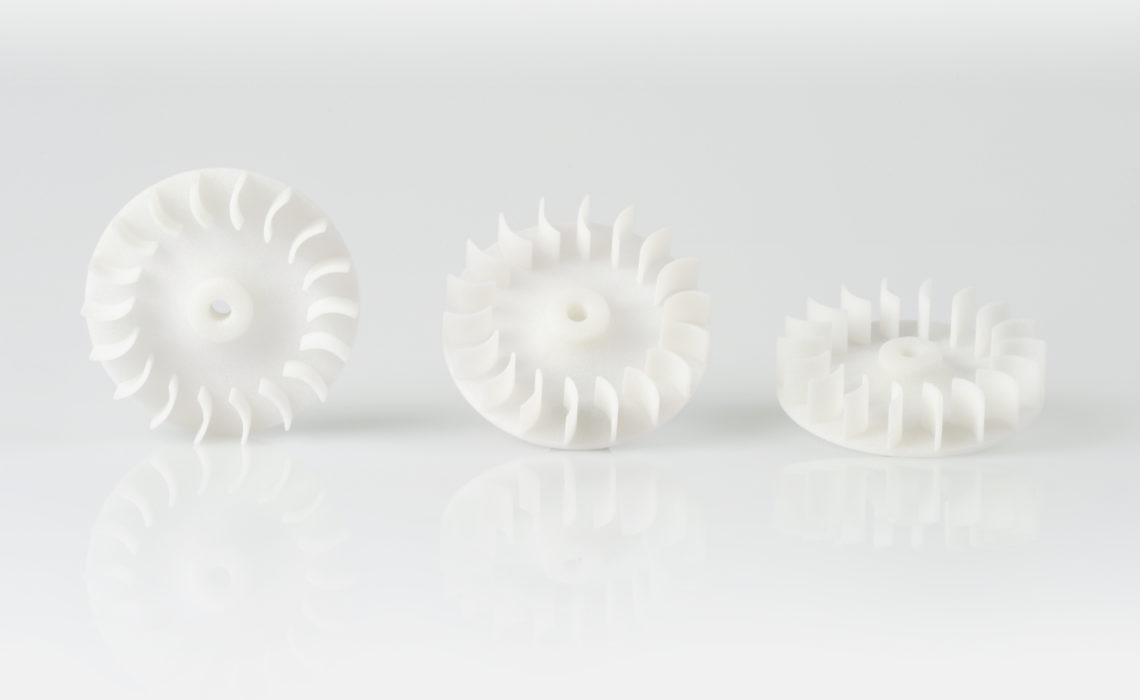
As 3D printing became more available around a decade ago, there was only a small number of industrial companies ready to embrace a powerful vision into the future of manufacturing. Now, the ability to transform and streamline production, along with deep diving into customization, has become a valuable tool for engineers designing prototypes and parts for applications in automotive, aerospace, medical 3D printing, and so much more.
Applications like Automotive Continue to Evolve with 3D Printing
In a recent webinar co-presented by Shapeways, Dr. Cary Baur, Manager of Polymer Material R&D, explained how the EOS Additive Minds team was formed to address the needs of industrial customers—and further, to understand what the real pull is for additive manufacturing in applications they use now and may look to in the future.
“At EOS, it’s my job to help develop our polymer technology and deliver it to our customers specifically working toward new applications,” Baur told Shapeways during the webinar. “I help drive our technology in that direction and enable those new applications via working together with you.”
All of the materials from EOS are powdered-based, and 3D printed with laser sintering—most commonly, Selective Laser Sintering—a technology that is extremely popular with Shapeways customers.

From Concept to Reality with Unlimited Freedom in Design—and Redesign
The focus at both EOS and Shapeways is working with customers to understand their manufacturing needs at any level. Baur points out that the EOS Additive Minds team is centered around finding tailored solutions for product development and then connecting with companies like Shapeways to transfer design and development into productive opportunities related to both manufacturing and business.
Freedom in design is what allows 3D printing to stand out over other technologies. It also allows for improvements on existing parts, as well as the creation of new products that were not possible before via traditional manufacturing. Lightweight materials allow for production of parts that are strong too, and suitable for dynamic moving parts and complex components.
“Now, we can lightweight parts that used to be very bulky,” said Baur. “We can also make custom lattices and things like that, and reduce the mass and material inputs drastically.”
The ability to take traditional parts or concepts and redesign them with 3D printing can be an eye-opener for manufacturers engaged in designing for a wide range of industrial applications.
Companies like EOS have seen great success in redesign for components for luxury, limited-edition cars, offering impressive price reductions for thousands of small parts that could have been made traditionally; in fact, ultimately they saw a 10-20% cost savings per transferred component. EOS has also streamlined designs for complex grippers, reducing parts exponentially, and even redesigning sports safety equipment like shin guards and helmets for much better shock absorption.
Rapid prototyping leads to much faster feedback and time to market, while customized 3D printing on demand has the potential to change the face of production altogether, leading to better quality, efficiency, and savings overall.

Harnessing the Transformative Powers of Additive Manufacturing
Baur’s Additive Minds team at EOS encourages designers to look at the development and production process more closely: Given our new design freedom, how can we look at this a different way? How can we start designing some of these components to fit in with each other, and how can we reduce the amount of input parts?
Functional integration leads to maximum productivity and cost optimization, allowing for embedded functionality without assembly, greater material efficiency, and no tooling costs. With the ability to take nearly a hundred parts and bring the assembly down to just one piece, it is obvious to see why 3D printing could surpass traditional manufacturing for production of complex parts eventually. This is also due to:
- Greater manufacturing agility
- Simplification for supply chain issues
- Shorter lead times
- The ability to personalize
Technology like Selective Laser Sintering specifically offers greater opportunities in design and production overall. Because unused powder acts as a bolstering system supporting parts during the printing process, there is no need for supports. That means engineers don’t have to factor in designing intricate supports for parts, and in the end, there is much less chance for damage due to added post-processing.
Hundreds of parts can be nested together in one build too. Shapeways uses proprietary purpose-built software to streamline and condense packing of parts, reducing the height of the build platform, saving materials, and accelerating production.
“Selective Laser Sintering can be used to distribute your manufacturing to digitize your product portfolio—leading to a lot of spare part reduction and a lot faster turnaround times for manufacturing,” said Baur.
The idea of on-demand 3D printing is beginning to appeal to more manufacturers as they realize the implications of how much time, space, and money they could save. With the ability to order parts and customize them when needed, businesses could feasibly say goodbye to large expanses of warehouse space and the expense, which soon may become outdated. That also goes for storing enormous numbers of spare parts and products, left sitting around waiting to be shipped at an unknown time.
The sheer magic of 3D printing revolves around disrupting traditional ways in manufacturing, along with shining a bright light on the infinite potential for innovation. The sky’s the limit in terms of how this transformative technology will eventually impact nearly every application, and continue to astonish us over the coming years in ways we never imagined.
About Shapeways
Contact Shapeways now to enjoy the benefits of advanced technology and materials for manufacturing creations with accuracy, complex detail, and no minimum or limits in terms of mass customization or single part orders. Shapeways has worked with over 1 million customers in 160 countries to make over 21 million parts! Read about case studies, find out more about Shapeways additive manufacturing solutions, and get instant quotes here.