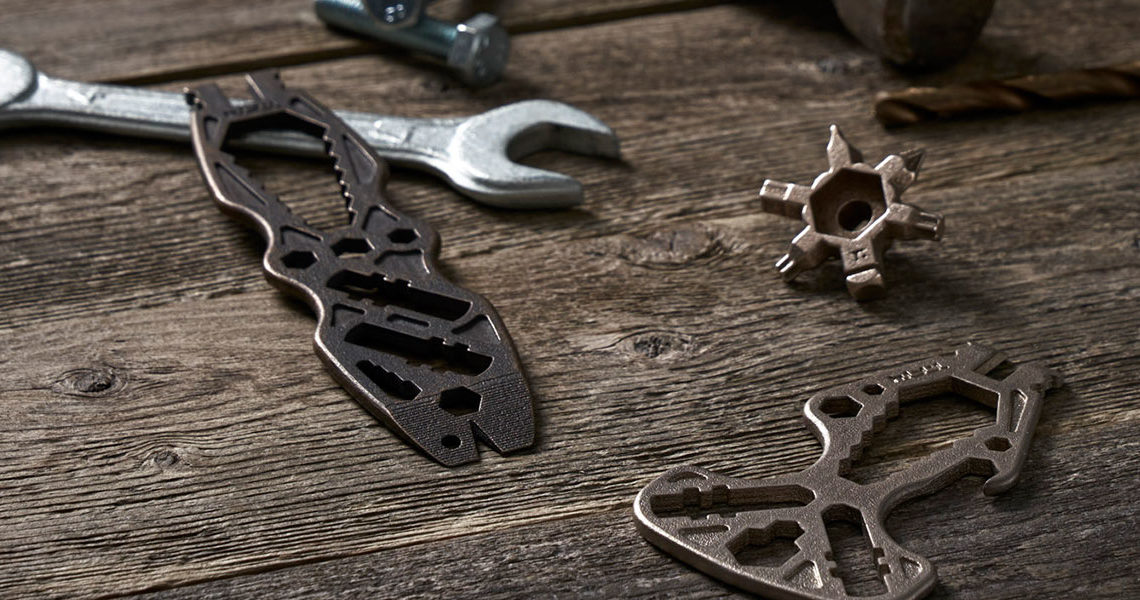
For decades the manufacturing sector has been dominated by a single manufacturing principle – the principle of subtractive manufacturing. Subtractive manufacturing solved numerous problems, becoming a dominant force in the manufacturing industry, all while building everything from nuts & bolts to complex automotive and aerospace components.
Around three decades ago we saw the invention of a new technology that challenged the traditional manufacturing process – the additive manufacturing process. Additive manufacturing technology has several striking advantages over the subtractive processes, like the time-to-market, costs savings for batch productions, design freedom, and manufacturing complexity.
While some have weighed the advantages of each technology against the other, engineers developed a new technology by combing the best of both subtractive & additive technologies in a single technology – Hybrid Manufacturing.
Hybrid Manufacturing
In the last decade, we’ve seen a rapid and unprecedented rise in the demand & supply of 3D printers across the world thanks to revolutionary predictions industry experts have made. There’s no doubt that 3D printing has shown unprecedented advantages over previous manufacturing technologies, but it also has a higher purpose to achieve.
Experts believe that 3D printing also has the ability to shape more advanced manufacturing technologies like hybrid manufacturing. Hybrid manufacturing is the combination of additive and subtractive manufacturing technologies, which can perform multiple manufacturing and post-processing operations on a single machine.
Additive manufacturing has ignited the spark and led engineers to think, design and develop hybrid systems. Engineers believe that a measured use of both additive and subtractive (more specifically, manufacturing by additive and post-processing by subtractive) will be the most focused approach to developing the hybrid systems of the future.
This is the central philosophy behind the development of hybrid manufacturing systems; a system that is not purely subtractive nor additive, but a perfect blend of both.
Hybrid Manufacturing: A Blend of Subtractive & Additive Manufacturing
By combining additive and subtractive methods, hybrid manufacturing takes advantages of both these technologies by blended them to eliminate their respective drawbacks.
For example, a hybrid system blends the advantages of CNC Machining like repeatability, precision, high-quality surface finish, and high productivity and those of additive technology, such as less material wastage, design and manufacturing freedom, and new material options.
By combining methods, the system can eliminate certain drawbacks of either method, making hybrid manufacturing a highly desirable proposition for manufacturers.
Types of Hybrid Manufacturing Technologies
While hybrid manufacturing is still a relatively new concept, a good deal of processes and machines are already out there. They can be categorized into the following types, depending on the process used.
Wire-Arc Additive Manufacturing (WAAM)
While the typical additive manufacturing processes use metal powder to add layers, the Wire Arc Additive Manufacturing (WAAM) technology uses a metal wire. This wire is melted using an electric arc. The melted wire, in the form of beads, is then deposited and stuck together creating a layer of material. This process is carried out repeatedly in a layer-by-layer form until the complete solid object is formed.
WAAM has predominantly been used for local repairs on damaged or worn components, and to manufacture round components and pressure vessels for decades. But with the advent of strong CAD/CAM suites and better knowledge of additive manufacturing technology, WAAM can now be used to build objects from scratch itself.
Additionally, in recent years, a lot of materials have been integrated into the process. As a general rule, any material that is available as a welding wire can be used in WAAM systems. Some prominently used materials include stainless steel, nickel-based alloys, titanium alloys, and aluminum alloys.
This technology has a wide range of applications in industries like aerospace, marine, automobiles, and architecture.
Directed Energy Deposition (DED)
Directed Energy Deposition (DED) technology is a common AM technology that closely resembles the Powder-Bed Fusion (PBF) process. Here, a laser is used to melt the powdered material. However, the process of powder deposition and its subsequent melting differs and is more cost-effective, making it easily scalable while producing larger parts.
Cold Spray (CS)
In a Cold Spray manufacturing technology, the solid-state coating is deposited to build products in a layer by layer fashion. This technology is mainly used in repairing damaged parts like those in marine and aerospace industries. It’s great for parts that undergo severe wear and tear, but cannot be discarded due to the heavy initial investment to produce them.
The advantage of Cold Spray technology is that there is no heat breakdown of the feedstock, making it so the technology allows retaining of the materials’ original properties involved and creating oxide-free deposits. It’s a new technology and its inherent benefits are garnering a lot of attention among the science and manufacturing communities.
Ultrasonic Additive Manufacturing (UAM)
In this path-breaking process, sound waves are harnessed to join layers upon layers of the metal stock foil. This process results in an actual metallurgical fusion, which can use several metals.
Hybrid Manufacturing Applications
Hybrid manufacturing has several diverse applications, including molds and tooling. It can also be used for part repair and maintenance applications.
However, the most popular application for hybrid lies in the aerospace and healthcare industry. The core reason is that both these industries rely heavily on industry standards and adherence to strict regulations. For new technologies like additive manufacturing, the technology, the process, material, printed part, and even the machine has to be qualified before it can be used in a real-world application.
Additive manufacturing has been quite instrumental in the early development of hybrid systems. This not only shows the versatility of the technology, but also the capability it has to accommodate itself and even other new technologies to augment the entire manufacturing process. The world may think that hybrid is the way forward but the core still remains firmly rooted in the additive manufacturing technology.