
One of the greatest benefits of 3D printing is the ability to cut out machining and tooling. With additive manufacturing, businesses can put a 3D design directly into production rather than experiencing long wait times. Industrial designers and engineers can rapid prototype and make changes to a 3D model with the click of a button–and they may also go on to manufacture high-performing, end parts with the same 3D printing materials and technology.
These days, both traditional and progressive manufacturers rely on 3D printing for tooling. 3D printed tools often complement or enhance the traditional manufacturing process–or may serve other utilitarian roles in applications like aerospace, automotive, medical, and more.
3D Printed Tooling for Molds and Master Patterns
Manufacturers produce molds with age-old, conventional methods for Injection Molding. 3D printing plays a large role in this process now too. Although a manufacturer can machine a traditional mold, 3D printed injection mold tooling can be made exponentially faster with the following benefits:
- Affordability
- Little to no lead time
- High resolution
- Exceptional quality
Users typically turn to molding for multiple (or mass) copies of a part. The 3D printed tool, in the form of a mold, acts as a vehicle for molten liquid, with the desired structure solidifying within.
Shapeways offers metal materials like Steel and Aluminum for 3D printing tools, along with other popular choices like Nylon 12 [Versatile Plastic]. This type of tooling, in the form of molds, can be used for mechanical parts as well as medical devices like prosthetics. Other materials for 3D printing tools like molds include Thermoplastic Polyurethane (TPU) and MJF Plastic PA12, serving applications like mechanical parts, cases, medical devices, and drone technology.
3D printed master patterns for molds with Urethane Casting are becoming more common too. The master pattern is the original from which countless replica molds can be made, filled with materials like polyurethane.

3D Printed Jigs, and Fixtures in Automotive Applications
3D printing is extremely useful for tooling jigs and fixtures, with a wide range of 3D printing materials available, from thermoplastics to metals.
From the most simple to complex designs, jigs play a critical role in industrial applications like automotive. This is true for digital fixtures too, serving as stationary parts and benchmarks in the assembly process, measuring and evaluating to confirm form and fit. 3D printed fixtures are efficient and economical, and helpful for spotting issues like warping or tolerance. These 3D printed tools can also be modified quickly during product development and testing.
3D Printed Cutting Tools for Industrial Applications
Whether using thermoplastics like Nylon 12 [Versatile Plastic] or metals like Steel, cutters are 3D printed with innovative parts like:
- Standard metal bodies
- Attachments
- Sheaths and cases
- Ergonomically designed handles
Larger cutting tools can be designed for greater balance, accuracy, and strength, but with 3D printing they can feature nearly any complex design that is also lightweight. Advanced 3D printing materials and technology can also improve the longevity and performance of cutting tools.
3D Printed Surgical Guides for Medical Applications
3D printing in healthcare has offered tremendous benefits, mainly because there is such positive impact on human life, improving quality–and in some cases even saving lives. Patient-specific treatment means that nearly the whole process can be customized for the individual, whether they are receiving a 3D printed implant or are having implants or prosthetics fitted.. Surgeons rely on procedure-specific 3D printed tools too, matching design, materials, and technology to the operation they are performing.
Examples of typical 3D printed surgical tools include:
- Clamps
- Forceps
- Handles for scalpels
- Hemostats
- Needle drivers
- Surgical trays
3D printed surgical tools and guides are usually manufactured in materials like Stainless Steel 316L or Nylon 12 [Versatile Plastic].
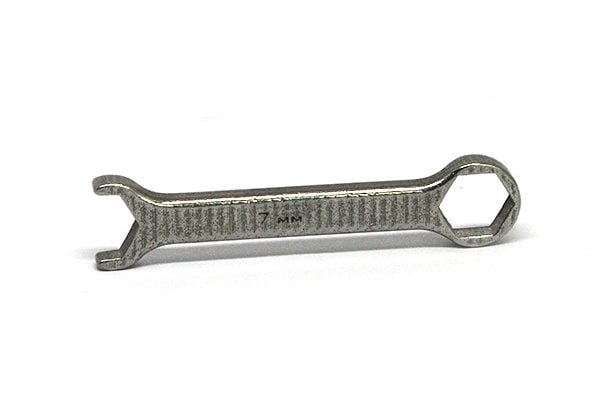
Soft Tooling vs. Hard Tooling
Soft tooling relies on creating a master pattern for a tool with flexible materials like silicone, while hard tooling relies on metal materials like Aluminum or Stainless Steel. Manufacturers tend to use soft tooling for prototyping, offering great surface finish, accuracy in detail, and swift turnaround for project deadlines.
Soft tooling via Urethane Casting is useful for prototyping and testing, creating models for important client presentations, and manufacturing in lower volumes. Small production runs with soft tooling make it easier to customize and modify parts and lead times are shortened. Overall, this technique is a better option for projects requiring speed but operating within budget constraints.
With hard tooling, there may be greater expense upfront, but the end products last longer. Hard tooling is also the better investment when manufacturing large volumes, despite the need for post-processing and further treatment after manufacturing.
Applications for both soft and hard tooling include nearly anything industrial, with large volumes of parts manufactured in aerospace, automotive, electronics, and medical. With a technique like Urethane Casting, manufacturers enjoy the ability to make a wide range of molds without being restricted to the expense and time-consuming process of making metal molds, typically more suitable for mass production.
3D printed tools are made quickly and economically, and can be modified and replaced with ease. They can also be 3D printed on-demand in any volume, demonstrating one of the greatest benefits of additive manufacturing with Shapeways. With the ability to store 3D printed tools digitally, products can be manufactured when the customer is ready–eliminating the need to keep inventory on the shelves gathering dust. Products can be customized as needed, and shipped directly to manufacturers’ customers.
About Shapeways
Enjoy the benefits of this advanced technology and a wide range of materials from Shapeways for 3D printing your creations with accuracy, complex detail, and no minimum or limits in terms of mass customization or single part orders. Shapeways has worked with over 1 million customers in 160 countries to 3D print over 21 million parts! Read about case studies, find out more about Shapeways additive manufacturing solutions, and get instant quotes here.