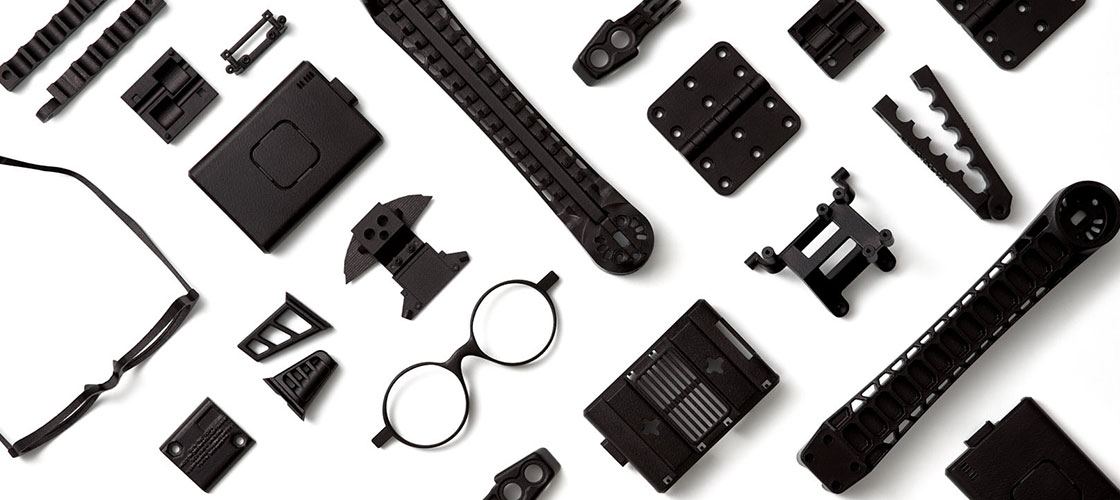
Precision is a key element for Shapeways designers. 3D design and 3D printing are centered around innovation, creativity, and the ability to create complex geometries which were previously impossible—but to achieve success in manufacturing, 3D printing tolerance rules (note: these really aren’t just suggestions!) must be followed.
3D printing is all about the details, and that’s especially true when it comes to tolerances. Defined as the acceptable amount of deviation in a 3D printed object’s dimensions, tolerances must be set correctly for success in additive manufacturing. Shapeways design guidelines often refer to this as the accuracy of a material.
Understanding Tolerances and Variations
While designers may upload 3D models with proper dimensions in mind, there are a variety of factors that can affect tolerances, including:
- Accuracy of slicing software
- 3D printer resolution
- 3D printing material properties
- Required post-processing techniques
Most 3D printing technology allows for a dimensional tolerance of at least 0.1 mm. These tolerances allow for more variation than most traditional manufacturing methods, like Injection Molding or CNC Machining. If deviations are too great, however, 3D prints may fail. Typically, Shapeways recommends tolerances between 0.15 mm and 0.3 mm, depending on project requirements and design rules.
The most common type of tolerance is dimensional tolerance, referring to the acceptable variations in 3D printed objects, while geometric tolerance refers to deviations from shape or structure, such as the angle of a corner.
Surface finish tolerances are critical too, in relation to the texture and appearance of the surface of the part. Factors like layer height, 3D printing speed, and support structures can all impact surface finishes; however, for some parts, aesthetics like surface finish may not be important for functional parts that will not be visible—allowing for faster, more cost-effective manufacturing without intricate attention to aesthetics of the part.
Optimizing Tolerance Settings
The impact of tolerances on 3D printed parts is not to be ignored, as these details significantly affect functionality and performance.
Tolerances that are too tight may not fit together properly or may be difficult to assemble, while tolerances that are too loose may result in unstable or faulty 3D printed prototypes or end-use products. In the face of major deviations, parts may fail completely due to lack of structural integrity or ability to hold up under stress.
The cost of production plays an essential role in most 3D printing projects, and tolerances are directly related. Tighter tolerances require more precise equipment and production, including more time and effort in manufacturing, raising costs. Looser tolerances yield parts that require less time and effort to produce, reducing costs. Still, lower quality and functionality can raise obvious concerns in terms of reliability and longevity of a 3D printed part.
To plan ahead during the design process, designers, engineers, and industrial manufacturers should keep the following suggestions in mind:
- Consult Shapeways design guidelines for specific material and printing technology being used to ensure that 3D models are compatible.
- Consider the intended use of the part, and whether it requires precise tolerances or attention to surface detail—depending on the application.
- Evaluate assembly requirements, based on size and complexity of the part.
- Include post-processing requirements while planning the design and production process in order to achieve the desired level of finish in the end product.
With these considerations in mind, 3D designers can optimize their designs and models to achieve high-quality, high-performing end products.