
Metal 3D printing and foundries have one thing in common: powerful manufacturing processes. While traditional methods like foundries may invoke the vision of darkly-lit factories decorated with basins of fire, 3D printing with metal is known for bringing modern, complex geometries to life out of seemingly nothing–and rapidly so–as well as offering the ability to insert itself into another technology or technique without taking it over.
An adaptation of the French word fonderie, which refers to casting metal, foundries are establishments designated for doing exactly that–harkening all the way back to the 1400s. Manufacturing would not be where it is today without foundries, responsible for the ongoing evolution of cast metal. Numerous production processes are usually running there simultaneously, relying on trade specialists responsible for many different tasks, from metallurgical engineers to coremakers, coresetters, grinders, and pourers.
The foundry is an endless source of metal products, all of which begin with a mold, traditionally created out of the most basic of materials, like sand. Foundries create master patterns from the first molds and then duplicate them, whether for low-volume or mass production. The traditional casting process then commences as molten metal is poured into the mold which was created from a master pattern with multiple models made available. Once the part has cooled and then solidified, casting is finished, and the structure can be removed.
The 3D Printing Foundry
Industrial designers and engineers commonly rely on age-old, traditional techniques like metal casting to make production of certain products possible; however, the same innovators are now also gravitating toward metal additive manufacturing materials within the same factories to summon forth what previously seemed impossible.
In keeping with the character of additive manufacturing overall, 3D printing for metal casting is definitely unconventional. Engineers may use a variety of advanced materials for 3D printing with metal, but the technology is actually used for pre-production purposes in creating versatile molds. 3D printing materials are available to foundries and have been used for years now, to include sand but also resources like wax, silicone, thermoplastics, and metals commonly selected like aluminum.
Shapeways offers a variety of different technologies for 3D printing with metal, including metal Binder Jetting and Material Jetting, as well as providing a range of resources to foundries for 3D printing molds. Specialized additive manufacturing services are also available for any project.
3D printed molds are used in foundry products related to applications like:
- Aerospace
- Automotive
- Construction equipment
- Critical mechanical parts
Increased freedom in design is a huge boon for industrial engineers 3D printing molds, as well as offering the ability to make more complex geometries. A wide range of materials are available, accessible, and in many cases, easily recyclable too.
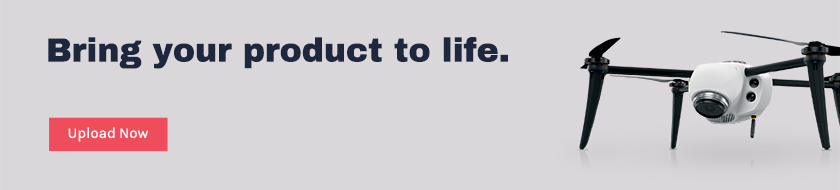
3D Printing Lost Wax Casting
Shapeways also specializes in Lost Wax Casting. For this technique, metal is accompanied by modern technology like 3D printing to make wax patterns for building plaster molds. Sprues are added so that metal flows through with the initial wax being melted and drained, further defining the term Lost Wax Casting. Once the metal cools and is solidified, the plaster is broken away from the mold. The metal product is detached, and from there, post-processing begins. This may include tumbling to polish the metal piece, or where applicable, it may be plated.
Shapeways metal materials for 3D printing Lost Wax Casting include:
Lost Wax Casting allows manufacturers to make professional-looking and innovative parts that are not possible with other techniques, along with creating complex shapes with interlocking parts and excellence in finishing. Find out more about the benefits of Lost Wax Casting with Shapeways here.
Additive Manufacturing with Metal Continues to be a Hot Trend
Many progressive foundries embrace 3D printing and the growing, related list of advanced materials already, allowing them to make even stronger prototypes and functional parts as metal manufacturing and metal 3D printing continue to be in high demand. This is especially true with Steel and Aluminum.
Popularity is trending in production overall and at Shapeways too, where the following metal additive manufacturing materials are available:
- Aluminum – Shapeways provides AlSi10Mgl for metal 3D printing, as a blend of aluminum, silicon, and magnesium. This material is used to make strong, highly functional parts and prototypes which help speed product development and enhance performance in applications like aerospace, drones, tools and fixtures, and structural components.
- Steel – This material is available in a variety of colors and finishes. Made up of 60% steel and 40% bronze, Steel is used for tools and accessories, home decor, and smaller industrial consumer goods.
- Stainless Steel 17-4 PH – Known for hard, tough material properties, this material is highly resistant to heat and corrosion, and offers high resolution. Manufacturers rely on Stainless Steel 17-4 PH for industrial manufacturing of jigs and fixtures, machine tools, pumps, valving, and fasteners.
- Stainless Steel 316L – This material is a single alloy, industrial metal known for corrosion resistance has high strength in low and high temperature environments. Stainless Steel 316L is used in applications like mechanical machinery to surgical tooling.
Most metal materials can be cast, leaving 3D printing and foundry work to intersect at any time, doubly improving a metal part that must be strong and unfailing; for instance, Shapeways activates the manufacturing process by 3D printing silicone molds for foundries. The molds are filled with the foundry’s choice of molten metal to shape important parts like pumps, valves, and brackets used for industrial engineering applications.
Foundries may turn to 3D printing technology for the same reasons other traditional manufacturers do, and nearly all of them can benefit from features like speed in creating molds that can be made in days rather than weeks or even months. Neither foundries techniques or 3D printing are canceling the other out anytime soon, so it makes perfect sense that they each complement the other–creating the perfect recipe for powerful parts–and taking that even further, resulting in higher customer satisfaction, quality in products, and longevity in high-performance systems where they may be installed.
About Shapeways
Enjoy the benefits of this advanced technology and a wide range of materials from Shapeways for 3D printing your creations with accuracy, complex detail, and no minimum or limits in terms of mass customization or single part orders. Shapeways has worked with over 1 million customers in 160 countries to 3D print over 21 million parts! Read about case studies, find out more about Shapeways additive manufacturing solutions, and get instant quotes here.