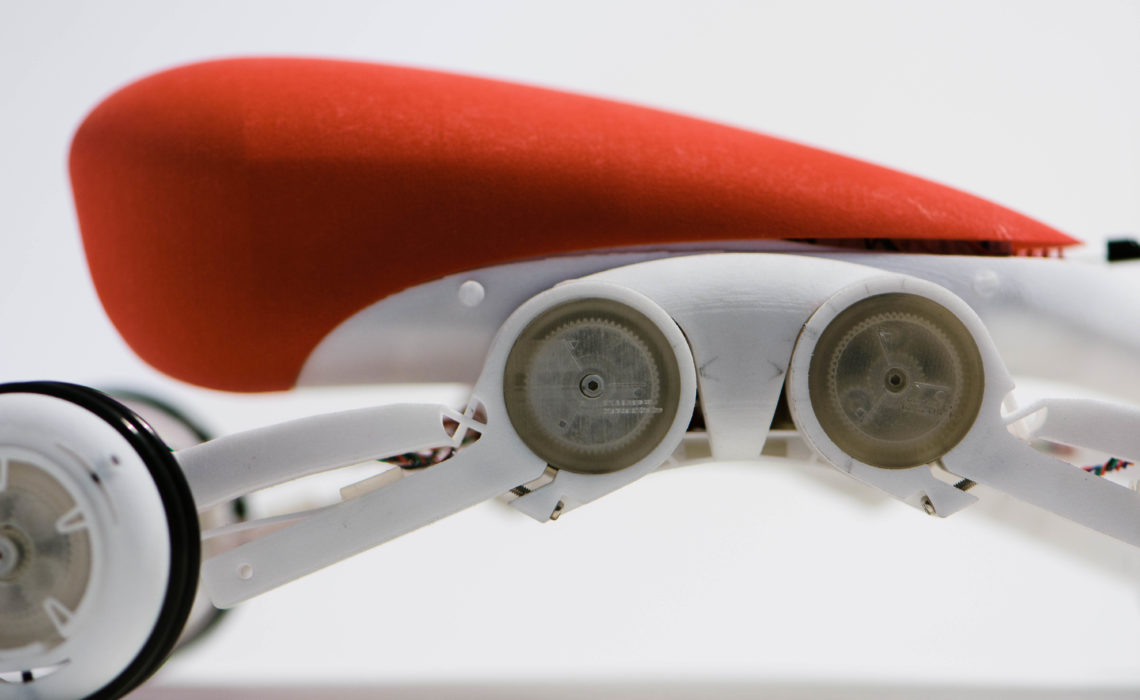
The task: Create an affordable gearbox to assist in robotics, wind turbines and other fields that could deliver a high reduction ratio. The challenge: Making them available via 3D printing in a simplistic way. But despite the inevitable obstacles that stood in their way, Nicolas Besuchet and Sugiyama Hiroyoshi were ready to tackle the project at hand.
“Although we were initially attempting to develop an interesting gearbox design by simply prototyping using 3D printing, we shifted to developing gearbox designs for 3D printing since the printed quality was just so damn good,” they told Shapeways.
The task at hand
Besuchet and Hiroyoshi, students at Waseda University in Tokyo, were not completely foreign to the world of 3D printing before tackling their thesis project, the 3Domnivore Robot. Besuchet had used the method of prototyping before, in fact, and knew it would be a great way to attack the trial-and-error process of their gearboxes.

Initial sketches of the 3Domnivore Robot
“3D printing with inkjet technologies enabled us to drastically reduce the size of our pieces and their costs. We then quickly found out that inkjet printing would give us sufficient resolution for creating miniature gears. Due to the fact that inkjet has a wax support material, this means that the pieces risk less of deforming themselves while being printed. In other words, through SLS nylon we discovered we could reliably print large parts while inkjet allowed us to achieve the same on a much smaller and cheaper scale.”
Setting strong goals in place
Once the Mechanical Engineering majors knew that 3D printing was the way to go, they laid out their main goals for the project. For starters, they wanted anyone to be able to 3D print the gearboxes. On a similar note, they wanted to show the complexities that can be designed through 3D printing. And above all, their main goal was to make a product that was cost-efficient and functional.
“Currently, high reduction gearboxes are in high demand in applications such as robotics, wind-turbines, and many more domains,” they said. “In robotics, for instance, a compact high-reduction gearbox (harmonic drive) can go up to $2000 for just one gearbox. With cheaper gearbox designs, one could envision affordable medical exoskeletons for example. Also, current solar panel farms employ expensive sun-tracking gearboxes which almost doubles the installation costs. This explains why sun-tracking is rarely used in solar farms. Yet with a cheap gearbox design, one could readily leverage sun-tracking to deliver an additional 40% solar energy capture boost.”
The inevitable bumps along the road
With their goals and mechanics in place, and the Shapeways EDU Grant to help fund and assist their project, Besuchet and Hiroyoshi were prepared to create the 3Domnivore Robot. Of course, the process came with its fair share of hiccups.
“This really was three projects nestled within each other. This made it very challenging to manage all that complexity. For instance, problems with our gearbox designs also impacted the completion of the robot. In the same vein, the 10 gearboxes of the robot [depended on] each gearbox and sensor to work very reliably—something which took us quite some time to achieve!”
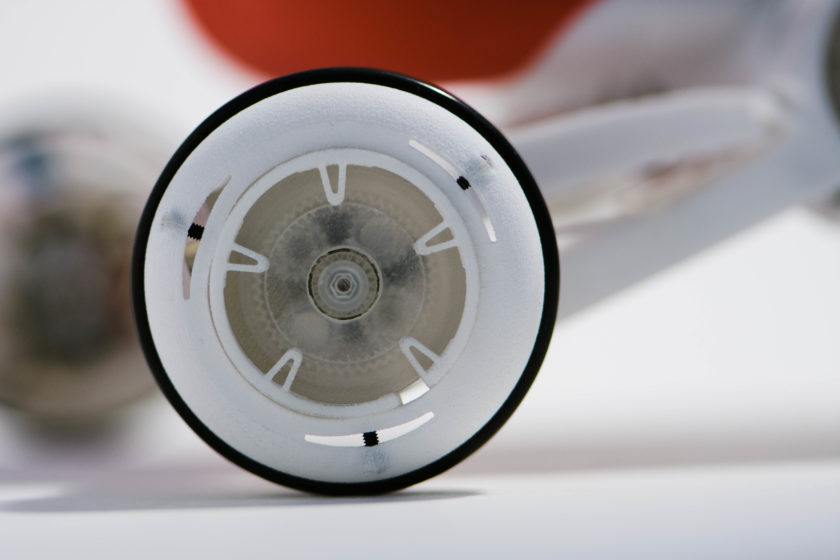
3Domnivore Robot wheel: Front view
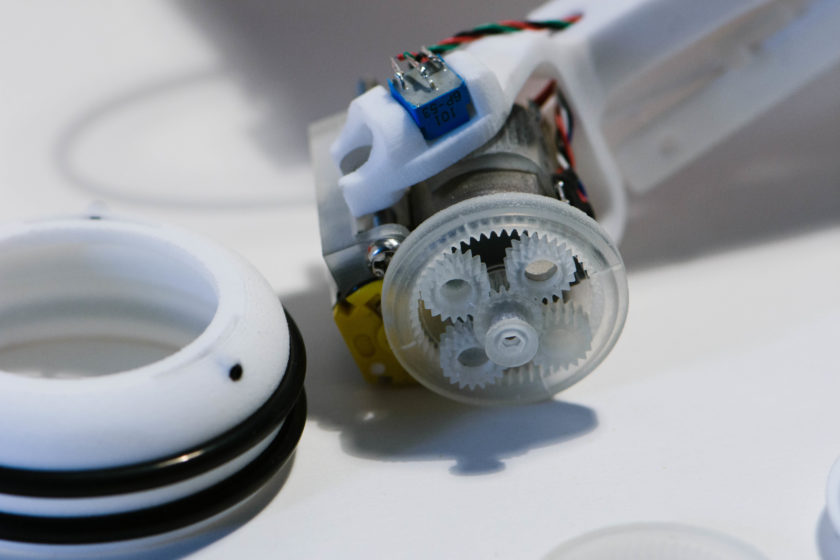
3Domnivore Robot wheel: Gearbox
But by pushing through the difficulties, interesting discoveries were made, particularly about the precision of 3D printing and design.
“The most unexpected discovery was how precise 3D printing had become. Just a few years ago, this entire project would have been unfeasible! We started off believing we would just be able to make some quick and dirty 3D printed prototype. We then discovered we could do quite clean and precise prototypes through 3D printing. And now, we’re starting to believe we could do pretty much any mechanism we want, provided that it be small enough to be sufficiently cheap and not impose excessive stresses on the material.”
Their journey with 3D printing has only just begun
In the end, the finished product was nothing short of awe-inspiring, something that both students were incredibly proud of. And although they may not plan to turn their project into a business, they hope their story inspires others, just as they were inspired to continue using 3D printing in the future.
“Back in the lab, we’re currently attempting a medical hip rehabilitation exoskeleton design which hopefully anybody could build with minimum tooling. There, we’re blending laser-cutting and 3D printing while leveraging on craftsmanship to keep the prices low. We’ve just completed the first prototype with promising results and are now preparing that design to be motorized. Again, the idea is to show the potential of 3D printing and laser cutting in democratizing mechanics.”
3D Print Your Robotics Needs
Learn how you can utilize 3D printing for robotics use. Contact us today to let us know how we can help.
Are you a student or a teacher?
You may be eligible for a 15% discount through our EDU program. Learn more.