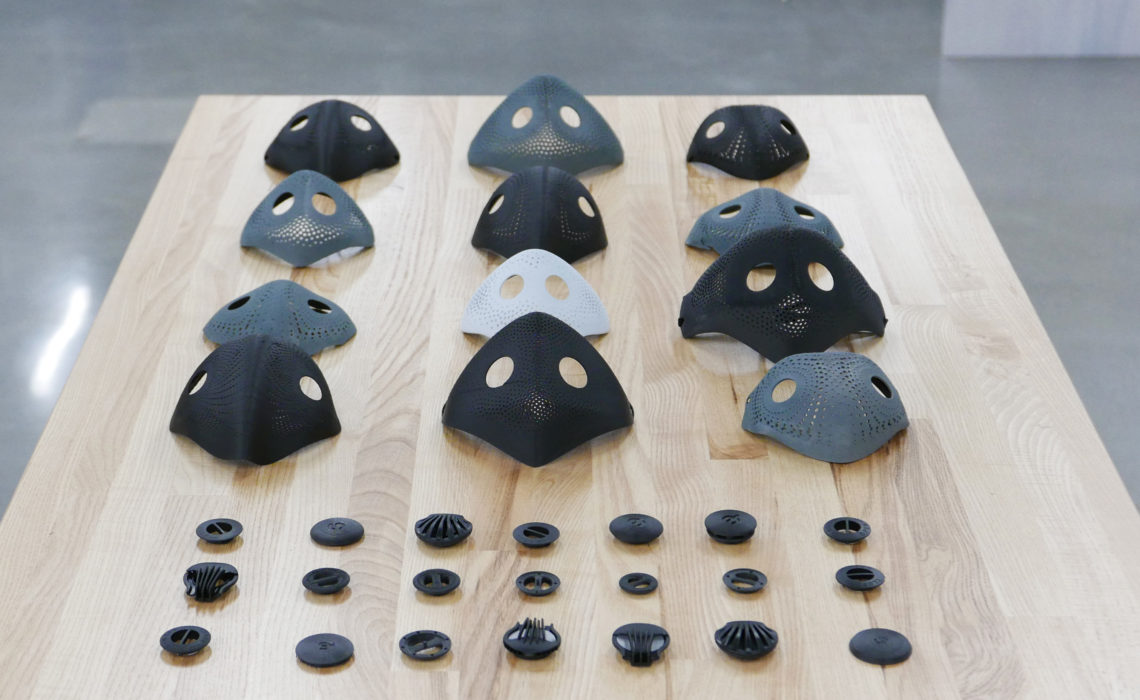
There are many ways to bring a vision to life, and the options continue to increase with greater depth for industrial designers and engineers. The additive manufacturing industry serves as a great example: 3D design offers the much-valued freedom to explore, create, and customize, and 3D printing sharpens product development to an extraordinary point–whether creating and testing innovative products–or breathing new life into existing ones.
Accelerate Time to Market with Additive Manufacturing
Rapid prototyping leads to faster production and accelerated time to market, but the process also gives designers expanded opportunities to customize and test intensively before they get there. In working with Shapeways, further constraints are removed too with no requirements for lead time. Designers can upload up to 20 3D models at any time, receive instant quotes and feedback regarding printability analysis, and enjoy the rewards of fast 3D printing.
Created in 1983 as a completely novel tool for engineers to speed up product development, 3D printing has far exceeded its original intended use, now highlighted in the mainstream for a range of innovative projects and end-use parts. A revolutionary process in its original form, resin-based Stereolithography (SLA), 3D printing was initially inspired by the common practice of using multiple layers of coatings to strengthen products. Decades later, 3D printing continues to propel engineers forward in applications like automotive, drones, medical, and far more–allowing them to create functional products never before possible with traditional manufacturing. Without the advent of or the accessibility to fast 3D printing, many manufacturers might still remain held back in product development.
In rapid prototyping, models can be 3D printed on demand for streamlined, ongoing feedback, allowing team members and customers to understand product features and details, as well as quickly noting any flaws or other issues that need to be resolved. Evaluations and modifications are made swiftly, and while numerous members of a team may be involved in the product development process, when it comes to making design changes and 3D printing new iterations, very little labor is required to make precise edits. No tooling is required, material usage is decreased, and many errors can be fixed instantaneously or avoided altogether with the 3D printing prototype.
Photorealistic, high-quality visuals make all the difference for product development, progressing from imagining and sharing a concept to holding a physical object. In a case like automotive applications, a car or motorcycle 3D printing prototype may be tested for form and fit repeatedly until it is flawless.

3D Print On Demand to Overcome Inventory and Supply Chain Restrictions
The freedom afforded to designers and manufacturers continues to play a large role in additive manufacturing. While advanced technology like Selective Laser Sintering (SLS) offers a wide range of new luxuries to designers and engineers, it also means that designers don’t have to worry about complexities and consequent possible headaches arising from support structures or rigorous post-processing exercises.
Looking at the larger picture, however, additive manufacturing is most disruptive and revolutionary. On-demand 3D printing allows for rapid prototyping of highly customized products in local areas. The supply chain is improved and further streamlined with this type of production and the ability to rapid prototype 3D printing, offering manufacturers greater command over product development, customization, personalization–and ultimately–distribution of finished products.
For smaller companies like Voytek Medical, known for their 3D printed medical clasps which organize equipment cords, the ability to prototype and 3D print end-use parts made a pivotal difference. Owner Steven Jaworski came to Shapeways after realizing his industrial prototyping and manufacturing needs had outgrown the capabilities of his desktop 3D printer. Developing a continued and long-term partnership with Shapeways, Jaworski has been able to iterate over the years without restriction.
“The business built the business,” said Jaworski. “I was able to scale as needed, and constantly reinvested back into the company. Any kind of profit went into expanding the product itself and getting better tools.”
Shapeways 3D prints Voytek parts with Nylon 12 [Versatile Plastic], relying on Selective Laser Sintering technology to create a ‘menu’ of 3D printed equipment cable organizers for hospitals to order.
Access Advanced 3D Printing Materials for Rapid Prototyping and End-Use Products
Growing numbers of Shapeways customers now prototype with one material that they go on to rely on for years in terms of 3D printing end-use products too. This is especially true with 3D printing materials like Nylon 12 [Versatile Plastic]. Known for incredible durability as well as adaptability, Nylon 12 [Versatile Plastic] is excellent for product development and long-term use. Because of this material’s high ductility, prototypes and parts can be made flexible for thinner parts, and more rigid for thicker 3D printed structures.
Materials like Multi Jet Fusion Plastic PA12 are also used in 3D printed rapid prototyping due to high strength and accuracy, and the same amount of design freedom offered through MJF with no need for support structures. Multi Jet Fusion technology is extremely well-adapted for prototyping due to precision in parts, as well as the excellence offered in surface quality and texture.
For prototypes that require finer details, designers often turn to SLA technology with materials like Accura 60, Accura Xtreme, and Accura Xtreme White 200. SLA 3D printing offers accuracy, good mechanical qualities, and also nice smooth surface finishes which make it a popular choice for designers making 3D printed rapid prototypes or end parts that require a more realistic look.
Find out more about rapid prototyping services with Shapeways here.
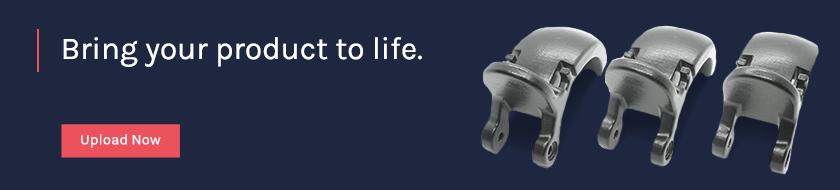
About Shapeways
Enjoy the benefits of this advanced technology and a wide range of materials from Shapeways for 3D printing your creations with accuracy, complex detail, and no minimum or limits in terms of mass customization or single part orders. Shapeways has worked with over 1 million customers in 160 countries to 3D print over 21 million parts! Read about case studies, find out more about Shapeways additive manufacturing solutions, and get instant quotes here.