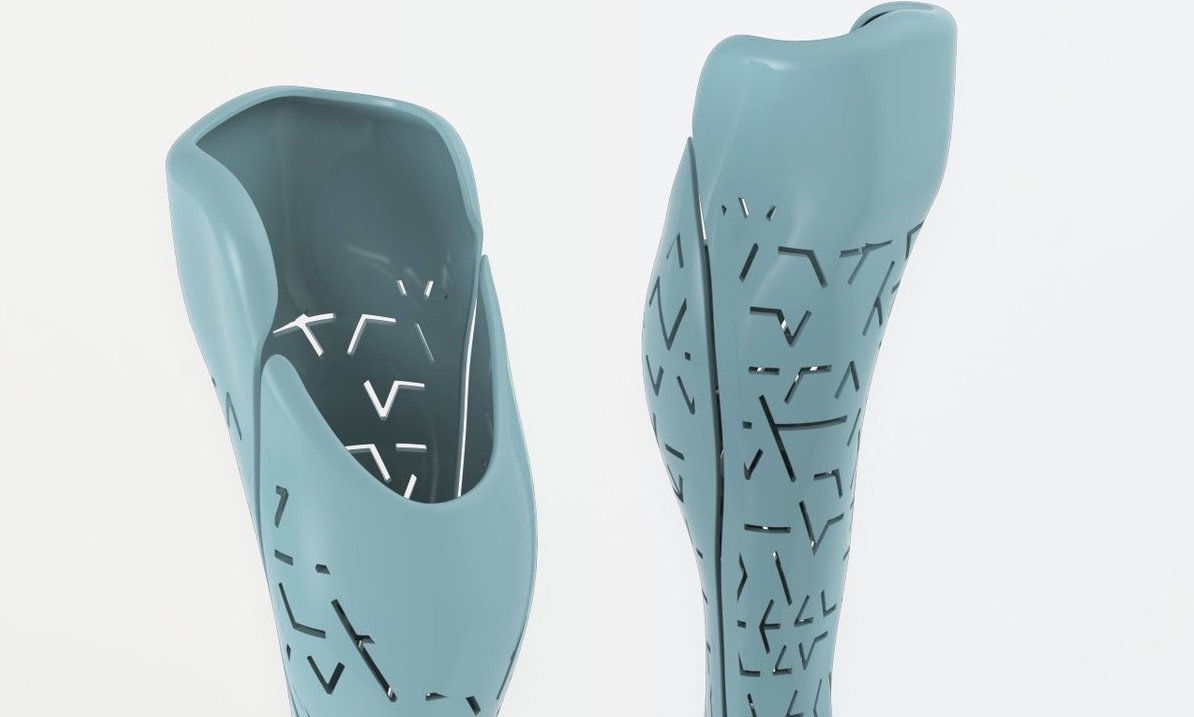
For nearly every individual who receives a conventional or 3D printed prosthetic, there is a story to tell. Whether patients were born with a need for limb replacement or required one later after a serious illness like a stroke or an all-too-common war-related injury, they may feel like everyone has given up on them at some point due to lack of functionality–and they may begin to give up on themselves after dealing with a long period of self-consciousness and frustration in not being able to complete tasks or enjoy a full life. The same is true for patients who may be suffering from limited or painful mobility before the use of 3D printed orthotics, or still, with those that have not been fitted properly. However, the innate desire to keep moving is found deep within most humans, no matter what the cost or time is spent in fabrication.
Prosthetics and Orthotics Have Come a Long Way
Artifacts serve as evidence of this need, harkening as far back as ancient Egypt; in fact the earliest known replacement device was an artificial big toe found on the foot of a mummy who had healed from an amputation and apparently not only used their prosthetic extensively, but was buried with it on. The rudimentary prosthetic device was dated between 1069 and 664BC, and impressively fabricated with linen, glue, and plaster.
Materials today are certainly more advanced, but the goal and the outcome are the same. Humans want to hold things, walk, and be productive just like everyone else; however, prosthetics and orthotics have exhibited a much less bespoke approach historically, and patients were less likely to wear them due to embarrassment as well as moderate to intense discomfort. Conventional methods, relying on Injection Molding or other types of common manufacturing are often more expensive and require more time spent in arduous fittings, iterating over long drawn-out periods of time, and less expedient production. In the end, delivery of the orthotic or prosthetic could take months.
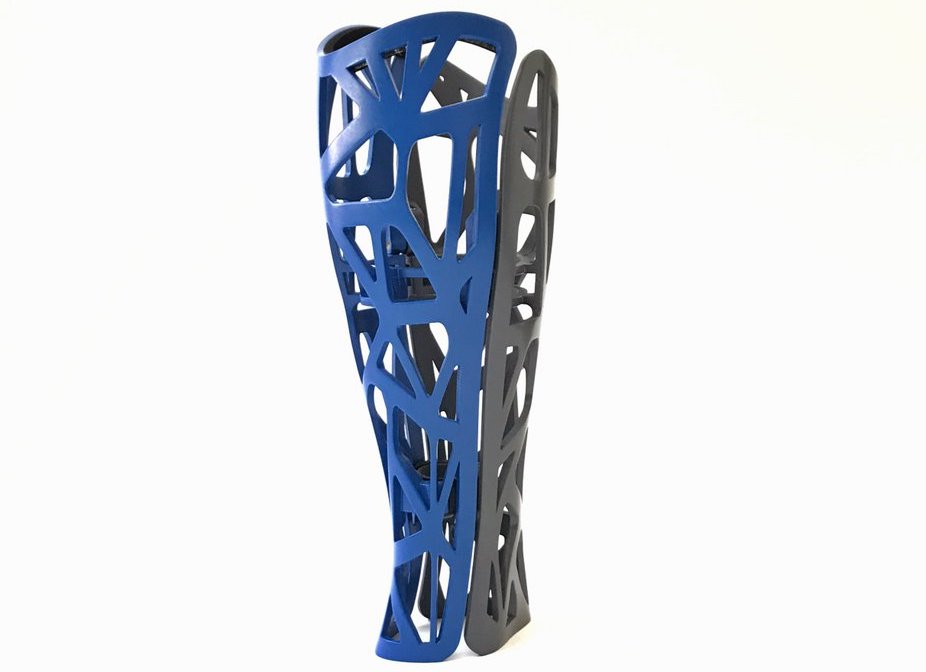
3D Printing Promotes Patient-Specific Treatment
With 3D printing, a quick 3D scan can be performed for creating a customized device that can be easily altered and printed again with quick turnaround and considerably less expense. Not only that, but for large numbers of such devices being made for adults and children in remote areas without easy access to medical care, 3D files can be easily transferred to individuals or doctors with 3D printers. The bottom line is that limb replacement and the production of orthotics is faster, more precise, and more accessible to everyone–answering the dreams of thousands who may have been waiting a very long time for a prosthetic or orthotic solution that is comfortable and appealing to wear.
Prototyping for Medical Devices
Although 3D printing has advanced far beyond rapid prototyping, with additive manufacturing responsible for a wide range of high-performance end parts today, the process is still extremely valuable for a process like creating prosthetics and orthotics. 3D printing is particularly valuable to this specific medical application not only because of the ability to transform people’s lives but also because 3D printing technology allows for complex geometries to be manufactured when they were previously impossible via conventional methods like CNC Machining or Injection Molding.
Medical teams, researchers, engineers, and designers rely on a host of features afforded through 3D printing, making it conducive to creating prosthetics as it is so easy to make a prototype and then iterate to whatever extent is required for a device like a bionic hand or arm. This also allows for intensive fitting of 3D printed orthotic devices, assuring comfort for the wearer without long wait times or great expense. For specialists like prosthetists, 3D printing is an incredible game-changer in terms of being able to design prosthetic sockets that rest between the patient’s skin and the device, where it is critical to have good fit and form. While previously the process may have been lengthy in terms of measuring, fitting, and creating a final product, 3D printing streamlines production from the first meeting with the patient–to their getting back to normal life and function.
Some prosthetics and orthotics are made solely through 3D scans and 3D printing, while others are complementary to robotics and bionics. Shapeways has worked with customers throughout the years producing prosthetic and orthotic parts requiring highly customized 3D printed sockets. Product development includes 3D printed models which are fitted to a tee and then manufactured for the final product that is often stylish, featuring different textures, as well as models like superhero motifs.
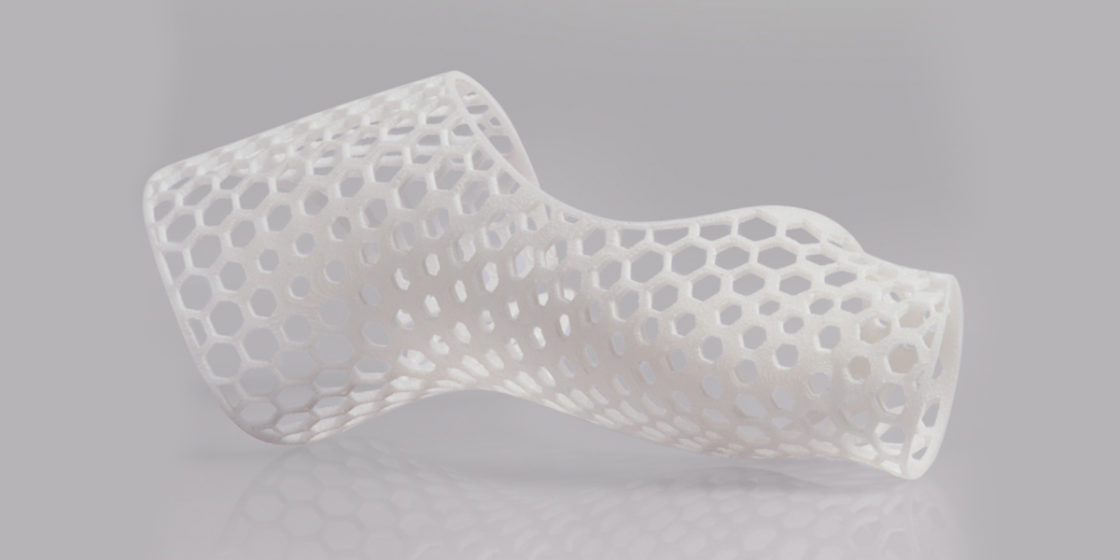
Additive Manufacturing for Orthotics and Prosthetics: Materials and Technology
Shapeways recommends the following 3D printing materials for prosthetics, all produced with Selective Laser Sintering technology:
Nylon 11 [PA11 (SLS)] – Most commonly in use for 3D printed orthotics and prosthetics for Shapeways customers, PA11 offers the required biocompatibility for products that will be in contact with human skin. This 3D printing material is also extremely durable and impact-resistant, available in natural white, with a standard finish.
Nylon 12 [Versatile Plastic] – Also biocompatible, this highly adaptable material is one of the most common materials in 3D printing. Very popular for prosthetics and orthotics, it is rugged and tough enough to hold up over the long term for wear. Nylon 12 [Versatile Plastic] is famous for its ability to act flexibly for 3D printing thin structures, and with rigor for 3D printing thicker parts. It can also be dyed in nine different colors and is available in a variety of 3D printing finishes, to include:
- Natural – This finish has a slightly rough surface and a matte finish.
- Processed – This finish removes some material to create a smoother surface.
- Premium – Using a mechanical process, ceramic media tumbling, this finish removes material to create a smooth surface.
- Smooth – This finish has a smooth surface and slight shine, created using a physio-chemical process to vapor smooth the surface.
Thermoplastic Polyurethane (TPU) – Used in many applications requiring elasticity and flexibility, TPU is a rubbery material popular for use in orthotics and prosthetics, to include design and production of sockets. As an industry-standard, TPU is recognized for its robust properties, lending strength and durability to medical devices, including those with interlocking features. TPU is available in off-white with a standard matte finish.
Selective Laser Sintering, a subcategory of powder bed fusion, begins as thin layers of powder are spread over the print bed. A powerful laser traces the design of the prototype or part on the powder, scanning each layer and fusing them together just under the melting point. No supports are necessary as unsintered powder bunches around parts being printed, stabilizing them during production. Unsintered powder can also be re-used, mixed in with virgin powder for the next round of additive manufacturing.
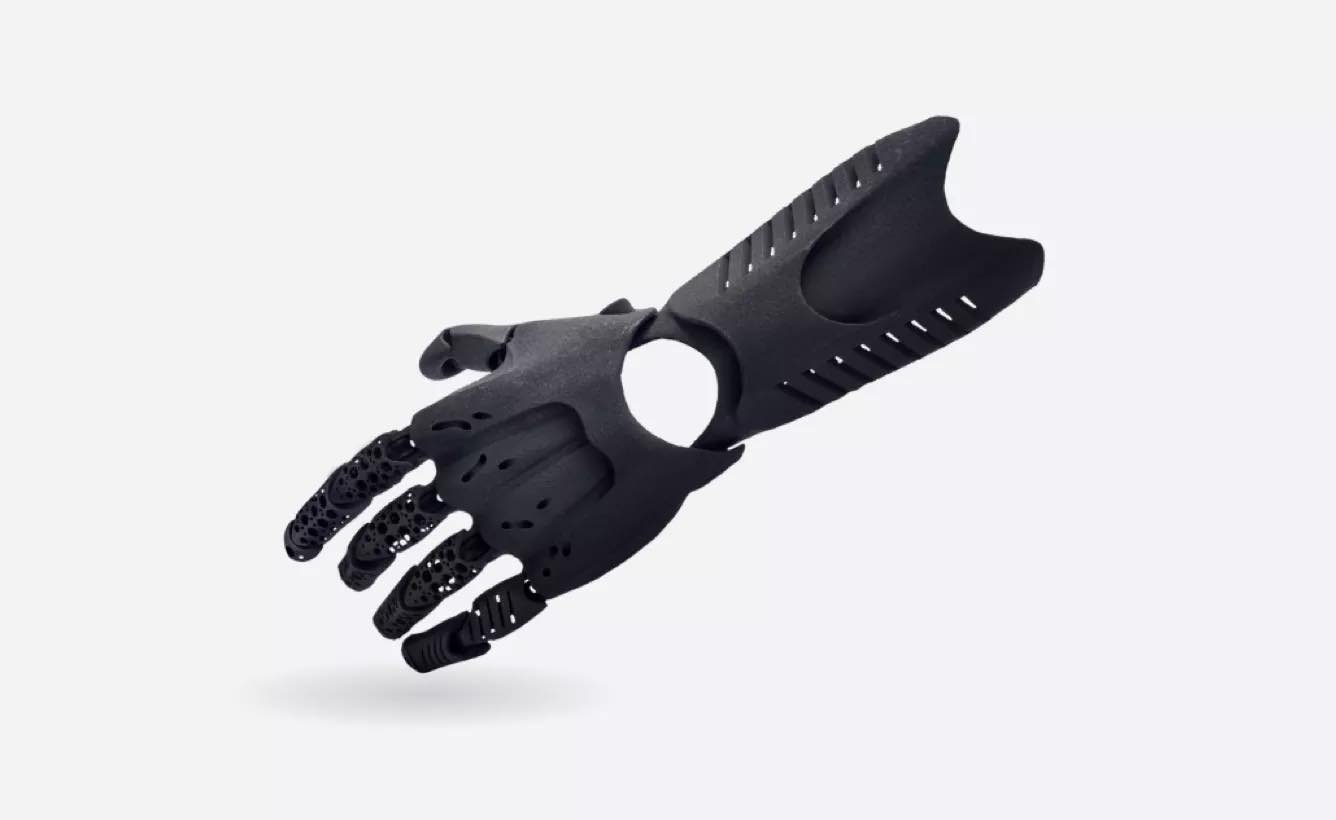
Global 3D Printing for Prosthetics and Orthotics
While continuing to lend a focus to customization and the best fit possible for wearers of 3D printed prosthetics and 3D printed orthotics, Shapeways partners with other manufacturers for production of market-ready 3D printed orthotics and prosthetics available to designers and businesses of all sizes.
3D printing is far more than just a viable process at this point, it is a normal option for progressive manufacturers who seek benefits like the speed and efficiency in production as well as the ability to produce geometries that were previously impossible. This is even more true in the prosthetics field where non-profit organizations like e-NABLE have banded together in international and community efforts to design prosthetics or download open-source designs and 3D print them for children and adults in need. They have produced thousands of 3D printed prosthetic designs and devices for use around the world, and often in areas that are war-torn or experiencing turmoil.
Other organizations have created fun prosthetics for children too; for instance, intensively customized 3D printed hands and arms featuring superhero style have been not only popular for kids around the world but extremely effective too. While traditional and less decorative prosthetics, 3D printed or not, may have made children feel self-conscious about wearing their prosthetics, devices outfitted to resemble superheroes have the opposite effect. Robotics and bionics are also integrated into a variety of different prosthetics, allowing limbs to function very much like a real limb–even allowing prosthetics wearers to play sports, musical instruments, and perform many typical tasks that the rest of us take for granted.
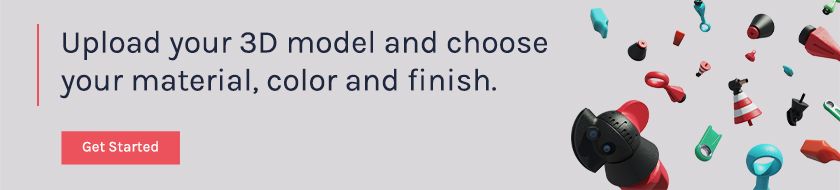
About Shapeways
Enjoy the benefits of this advanced technology and a wide range of materials from Shapeways for 3D printing your creations with accuracy, complex detail, and no minimum or limits in terms of mass customization or single part orders. Shapeways has worked with over 1 million customers in 160 countries to 3D print over 21 million parts! Read about case studies, find out more about Shapeways additive manufacturing solutions, and get instant quotes here.